CELRe®
木の持続可能性とプラスチックの利便性のハイブリット材料
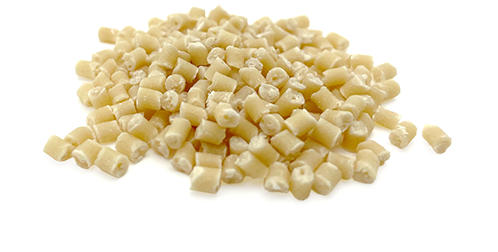
自然と共生する樹脂、
プラスチックのあたらしいカタチ
埋め立てない、再利用できる材料を未来に
古河電工の CELRe® 製造プロセス
当社が光ファイバケーブルや電力ケーブルの製造などで培ってきた樹脂混練技術を活かして、パルプと熱可塑性樹脂を二軸押出機で混練、ワンステップでマイクロオーダーのセルロース繊維を樹脂中に高分散させる技術を確立し、強度と耐衝撃性を両立したセルロース繊維強化樹脂CELRe®を開発しました。
従来、セルロース繊維は樹脂への分散が難しく、ナノ化や疎水化のプロセスを経ることから製造コストが高く課題となっていましたが、CELRe®本開発品ではセルロース繊維のナノ化や疎水化を経由せず、熱可塑性樹脂にセルロース繊維を直接分散する独自プロセス(図)により、必要とするエネルギーが少なく、低コストで製造が可能です。
セルロース繊維を51%含有するCELRe® KCPグレードの他、強度と耐衝撃性を両立したCELRe® DFグレードを展開します。
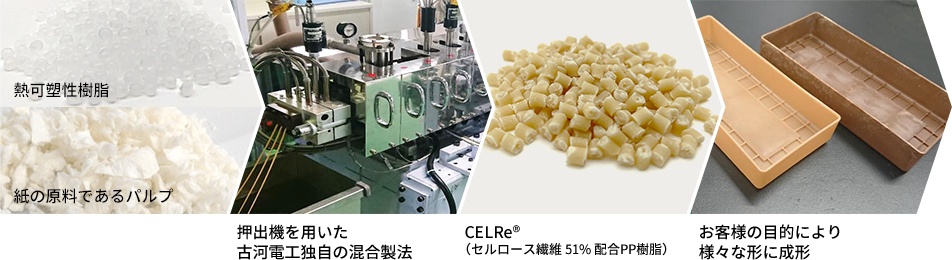
CELRe®の特長
独自技術でセルロースを樹脂中に高分散
(注) μm:マイクロメートル(ミクロン)、1/1000mm
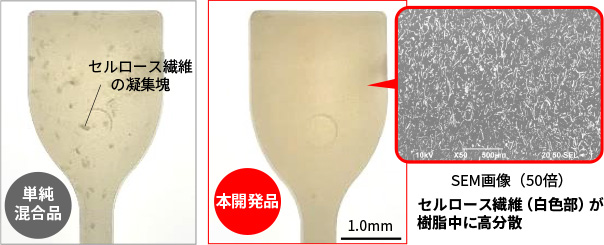
従来設備で成形が可能
当社設備や協力会社での成形テストを実施
従来の熱可塑性樹脂と同様に成形加工できることを確認しています。
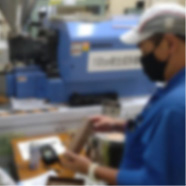

独特の風合い(プレス成形)・着色が可能
製品のCO2削減に貢献
製品のカーボンフットプリント(Carbon Footprint, Cradle–To-Gate)
原材料および製品の製造に関わるCO2排出量を計算しました(材料輸送時のCO2発生量は含みません)。
ナフサを原料とする樹脂材料からバイオマス材のセルロース繊維に置き換えることで、石油資源の節約とCO2排出量削減に貢献します。
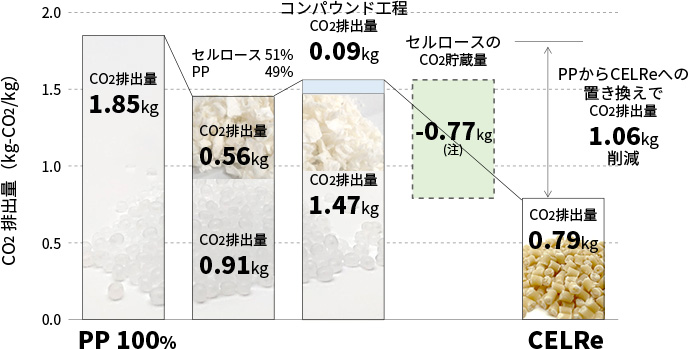
(注)
セルロースは41%が炭素であり、1.0kgあたり1.5kgのCO2を貯蔵しているとみなせるため、セルロース繊維製造時のCO2排出量1.1kgから上記1.5kgを差し引いた値を用いて計算しています。
CO2排出量の数値は、以下の文献の値を使用しています。
S.V. Joshi et al., Composites: Part A, Vol.35 (2004), p.371-376
Boland et al., Journal of Industrial Ecology, Vol.20, Issue1, February 2016, p.179-189
S. Nakayama et al., 紙パ技協誌, Vol.56 (2002), No.7, p.1035-1046
マテリアルリサイクルが可能
CELRe®は粉砕時のセルロース繊維の切断による材料の強度低下が起こりにくいため、マテリアルリサイクルが可能な低環境負荷材料です。お客様の製品の資源投入量・消費量を低減し、サーキュラーエコノミーの実現に貢献します。
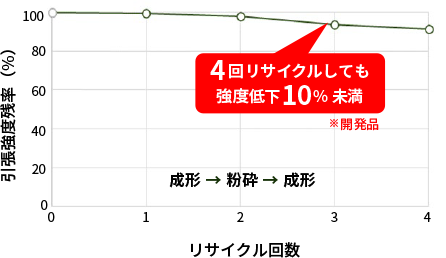
成形工程のクローズドループリサイクルが可能
お客様でのCELRe®成形時に発生する端材(例えばスプールランナー)を粉砕し製品に戻しても強度低下がほとんどなくクローズドループリサイクルによりCO2排出量削減、材料コストの削減に貢献します。
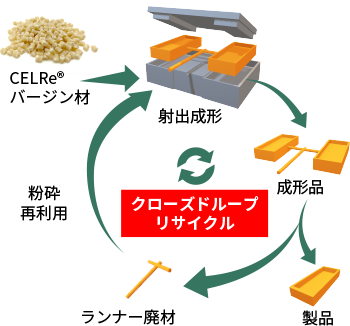
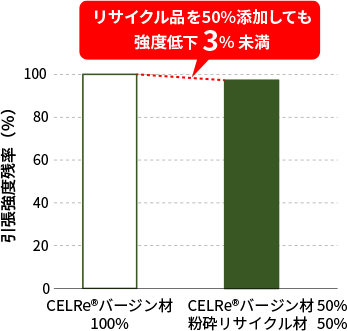
強度と耐衝撃性を両立したDFグレード
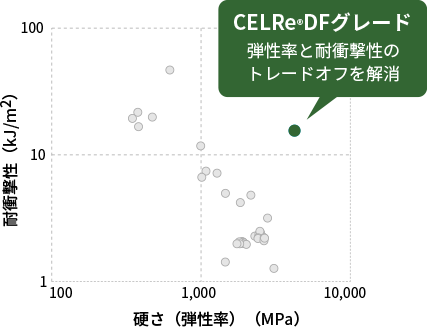
バイオマスマーク50を取得
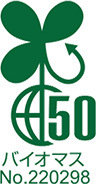
お知らせ
-
2023年9月25日展示会
-
2023年5月19日展示会
-
2023年5月19日ニュースリリース
-
2023年5月19日お知らせセルロース繊維強化樹脂「CELRe®」のサイトをオープンしました。
お問い合わせはこちらからお願いします。