以2050年实现碳中和为目标。通过轻量化和防腐蚀技术发起挑战的古河AS铝电线和α端子
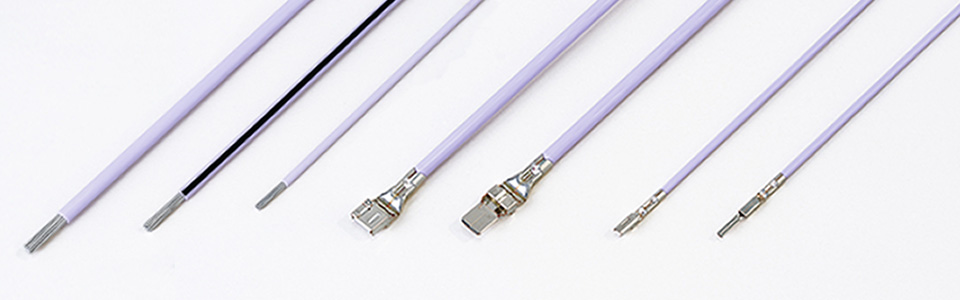
汽车已成为我们生活中不可或缺的一种交通工具。最近,为了支持更安全、放心且舒适的出行,汽车开始配备各种设备。与此同时,为了实现碳中和社会,减少CO2排放,人们对汽车轻量化的需求也日益增加。为了满足这些需求,古河电工集团主要从事汽车电子产品开发和制造的古河AS一直在致力于挑战技术开发,以实现汽车内电线的轻量化。
※ “α端子” 是古河电气工业株式会社和古河AS株式会社的注册商标。
实现汽车轻量化和制造过程低碳化!古河AS的“铝线束”是什么
近年来,汽车领域出现了各种发展,包括搭载驾驶辅助系统以减少交通事故,实现自动驾驶技术实用化以解决少子老龄化社会中的司机不足问题等。此外,随着EV(电动汽车)的普及,搭载大容量电池等的车体重量也呈上升趋势。因此,人们开始关注连接汽车内的电子设备和电池等的线束轻量化问题。古河AS通过使用铝制线束实现了车体的轻量化,从而帮助实现去碳化社会。
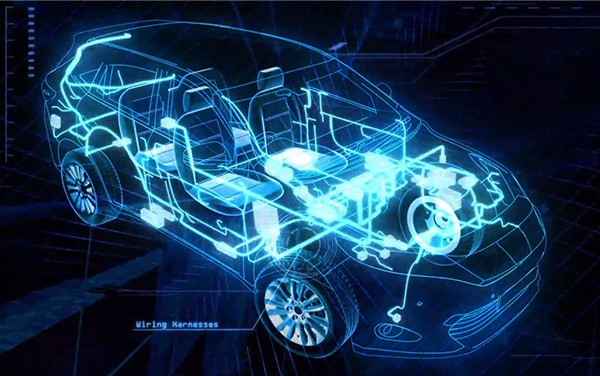
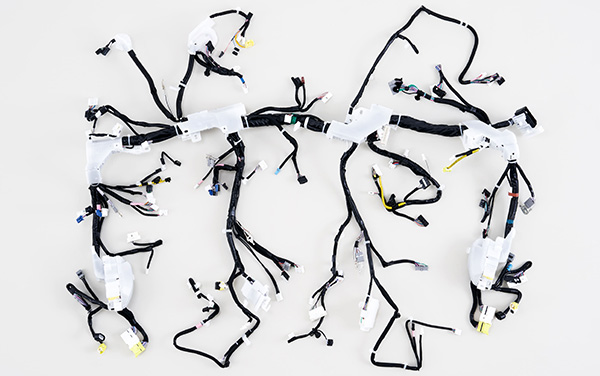
传统上,线束使用的是铜电线作为导体,每辆普通汽车的线束重约20kg,而大型SUV甚至重达约50kg。然而,如果使用铝作为导体,由于其比重约为铜的三分之一,因此线束的重量可以减轻超过10%。
古河AS的铝线束采用了在铝电线和铜电线分别与铜端子进行组合的结构,然而在其制造工艺中,铝的加工在使用水力发电的海外工厂进行,而铜的加工则运用了日光事业所的水力发电和三重工场的太阳能发电。此外,在电线和端子的连接工艺中,不仅利用太阳能发电,还利用地热发电,从制造阶段开始,始终坚持环保制造。
采用独创的焊接技术实现的“防腐蚀”是产品的关键
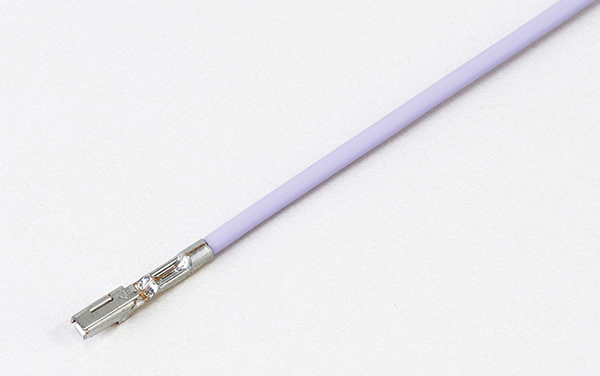
首先,将电束中使用的铜电线替换为铝电线的轻量化方法在开始搭载电动车窗等电机时便已经被行业各家公司考虑过。然而,通常情况下,不仅是电线,将连接电子零部件的端子替换为铝也较为困难,因此需要连接“铝电线”和“铜端子”等不同的金属。
这里的关键问题是金属的防腐蚀。当连接不同金属时,接触部分若附着水分可能引起“异种金属接触腐蚀”这一化学现象导致的表面腐蚀,而防止这种情况发生是一个重要课题。
对此,人们最初考虑采用树脂来完全覆盖铝和铜的接触部分以防止水的渗入。然而,采用这种方法会增加一道线束的制造工序,成本也会相应增加,因此线束的铝化一直被认为是一个难题。
为了一举解决这些课题,古河AS于2012年启动了一个项目,使用焊接技术将铜的端子形成为密闭管状,并将铝电线紧密压接在其中,从而开发不需要使用树脂的防腐蚀功能的新型端子“α端子”。
而铜也被用于散热零部件,具有高热传导率和热能易于扩散的特点,因此焊接非常困难。对小型端子运用焊接技术本身也是一种新的尝试,因此,古河电工集团动员了整个集团的知识和技术来挑战开发。
通过运用古河电工集团迄今为止在光通信领域积累了各种先进技术(光纤、半导体激光、光熔接技术等),同时结合通过高集光性实现高能量密度的公司自制光纤激光振荡器以及独自开发的高精度三维激光焊接技术,实现了高速冲压和光纤激光焊接的在线一体制造技术。此外还成功开发了通过光纤激光焊接形成管状的铜制端子以及紧密压接铝电线的α端子。
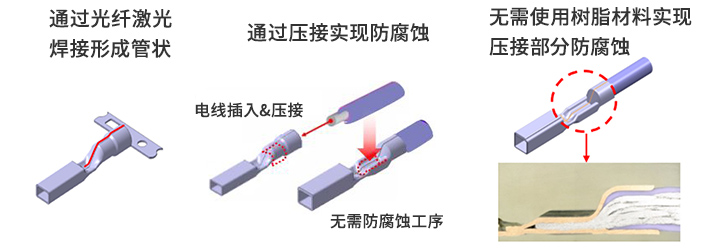
α端子于2015年建立了稳定的量产体制,每分钟制造数量大约为数百个。客户为这种精密且高速的制造技术而感到惊叹。
此外,随着车体的高功能化,线束数量增加,从而也增加了在车内饮食或产生露水等情况下线束与水发生接触的风险。即使在这种情况下,α端子仍然能够发挥作用,其高度的防腐蚀技术再次得到了高度评价。
进一步挑战以实现汽车的碳中和目标
汽车行业今后有望迎来进一步的发展,尤其是政府宣布“到2050年,在整个汽车的生命周期内实现碳中和”的方针后,EV在日本的发展势头将更加迅猛。
相对于使用汽油等燃料并通过发动机行驶的ICE(内燃机)车,EV(电动汽车)采用电能作为动力源,通过电机驱动行驶。因此,EV用电机需要具备足够的耐久性,以承受大容量的电流。这也导致了连接高电压电池和EV用电机的电线需要更大(更粗)的尺寸。然而,电线变得更粗意味着它会变得更硬,这导致了线束的柔韧性受到影响,布线上也会更困难。
因此,古河AS正在利用古河电工集团的聚合物组合技术,以实现同时具备耐热性和柔韧性等功能的电线,从而支持EV等电动汽车领域的扩张,为汽车的碳中和贡献力量。
此外,公司未来还将计划着手处理线束的再生利用。目前,线束中使用了各种不同种类的金属和树脂,但将它们完全分拣和回收在技术和成本上都存在困难,线束再生利用的技术和机制尚未建立。因此,当前的目标是开发一种技术,将废弃的线束再次转化为可用的线束。这将进一步为实现2050年汽车的碳中和贡献力量。