Creating added value through a combination of history and new ideas. Story behind the development of the “fusion splicer”, an essential device for connecting optical fiber
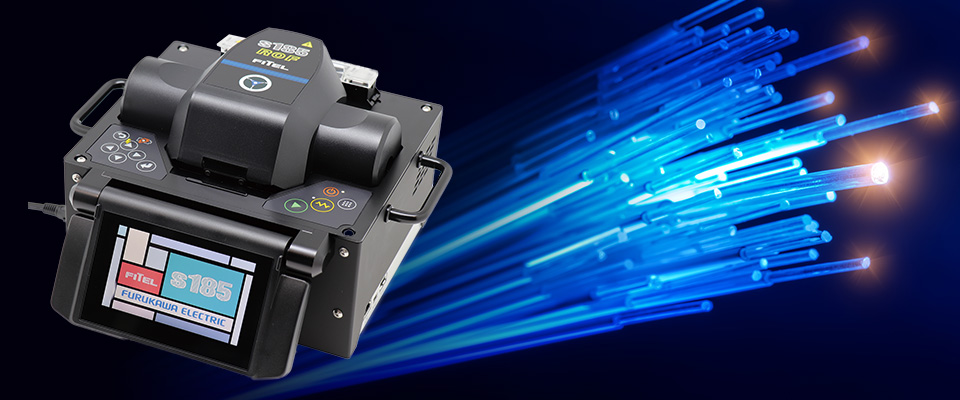
The Internet we use every day without much thought is supported by a network of underground and submarine optical cable through which the data passes. In addition to optical fiber that can transmit even more data, Furukawa Electric is focusing the development of “fusion splicing devices (hereinafter “fusion splicer”)” that are important for connecting these fibers. The process was one challenge after another. Let’s take a look at the story behind the development of the fusion splicer.
Multicore fiber forms the arteries of the digital society and supports large volume data communications
Communication using the Internet has become important infrastructure that is essential for daily life, including Internet searches, social media, watching videos and online meetings and classes. The volume of data travelling through the Internet has rapidly increased in recent years. As a result, the optical fiber that supports the Internet also needs to have further increased capacity.
As the name suggests, optical fiber is “fiber that transmits light”. It contains a core made of glass or plastic that transmits light. Traditionally, most optical fiber products were single core, which means there was one core in each fiber. However, in recent years, “multicore fiber” has been developed with several cores in each fiber to make larger volume data communications possible.
General-use optical fiber conforming to international standards has a diameter of 125μm (0.125mm). This is the same thickness as one strand of hair. Multicore fiber normally contains 4-5 cores with a diameter of 10μm each, and fiber with a slightly larger diameter contains 19 cores. It is planned to install this fiber mainly as long-length submarine cable.
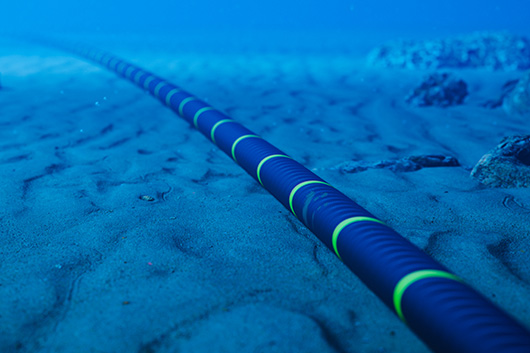
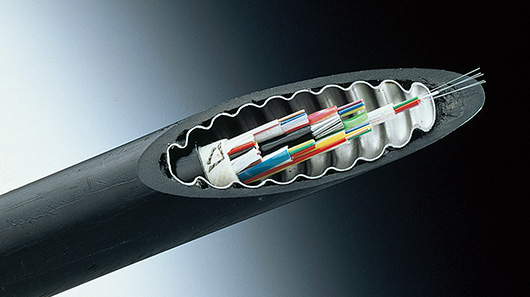
Delivering data to distant countries requires extremely long optical cable installed on the seafloor. However, the maximum length of optical cable that can be manufactured at the factory is slightly less than 100km. Therefore, in order to link Japan and the West Coast of the United States, a distance of about 9,000km, it is necessary to connect the optical cable and the optical fiber inside a total of 90 times. A device called a “fusion splicer” is used for these connections.
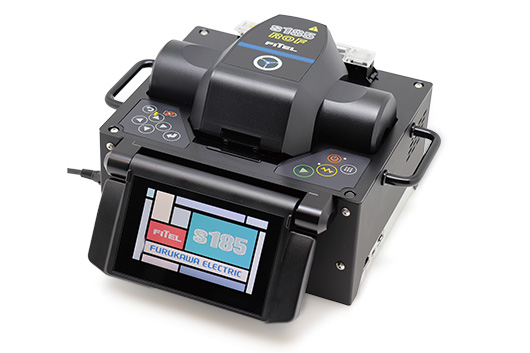
First challenge was “100% correct fiber connections”
Furukawa Electric had already developed and manufactured fusion splicers for single core optical fiber, but developing a fusion splicer for multicore fiber was extremely difficult and involved a number of challenges.
Fusion splicers heat the ends of two strands of abutting multicore fiber, and the fibers are connected by the surface tension generated when the ends melt. The cross-section of multicore fiber contains a “marker” that is smaller than the cores. Using this marker as a guide, the individually numbered cores are connected, but when connecting the cores, it is necessary to ensure the fiber is aligned correctly. If the cores are not aligned exactly, light leaks from the connection, reducing the intensity of the light and decreasing the transmission speed.
However, talking about “connections” is simple, but the real challenge is accurately connecting cores arranged within a fiber that is the same thickness as a human hair. The development team needed to create an extremely high precision fusion splicer.
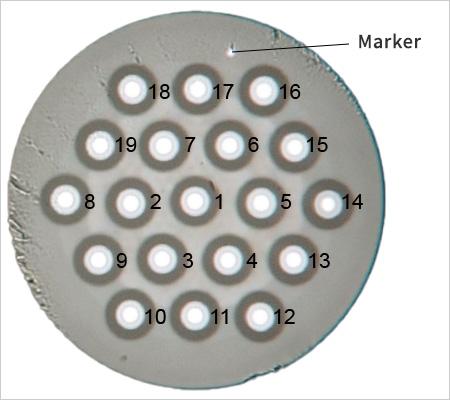
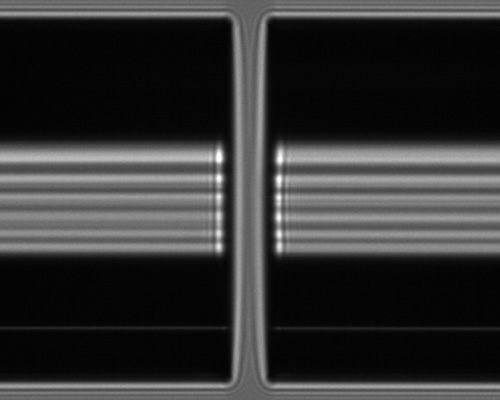
The first challenge faced by the developers was “how the fiber should look” when connecting multicore fiber. Because multicore fiber has a complex cross-sectional structure, it was unknown how the fiber should look in order to ensure accurate fusion splices.
In response to this, the development team commenced a light tracking simulation. While rotating the multicore fiber, light was applied from the side, and data on the transmitted light was obtained. Based on this data, technology for identifying the position of the marker and cores was developed using image analysis, and it was possible to grasp “how the fiber should look” when connecting multicore fiber.
Also, the images recorded when actually splicing contained various noise, but because the “way the fiber should look” was already known, it was possible to establish a method for eliminating this noise.
In addition, multicore fiber is still in its infancy, and the structure has not been standardized. Therefore, the dimensions of the fiber manufactured by each manufacturer differ slightly, and this was also an issue. Despite issues such as this, because the “way the fiber should look” had already been identified, it was possible to successfully minimize the impact on splicing.
Ideas provided by young engineers became hints for development, and their fresh perspectives, which surprised even the veteran engineers, opened the way forward to development, and the team as a whole had high motivation.
※(融着中:Fusion splicing, 診断中:Analyzing, 一時停止:Stop)
Another hurdle was “reducing splicing time”
In this way, Furukawa Electric’s fusion splicer achieved 100% core position recognition in multicore fiber, but the next issue to be addressed was “splicing time”.
When installing multicore fiber in actual telecommunications worksites, short splicing time is a requisite. The longer each splice takes, the longer the overall project will last, resulting in higher costs, such as personnel expenses.
However, when gathering a lot of information and performing a number of calculations in order to accurately connect multicore fiber, it takes a long time to complete the image analysis. Splicing single core fiber takes about 10 seconds per fiber. Compared to this, during early development in the summer of 2021, it took 24 minutes to splice a multicore fiber. This result was still far from the level required for commercialization.
The development team set the goal of reducing the 24 minutes by at least 90% and worked to reduce the splicing time. Through numerous innovations including improvements to the calculation method for image analysis, less than 2 years following the first successful splice, it was possible to reduce splicing time to 1 minutes 30 seconds in the spring of 2023. Today, research continues with the aim of reducing the time it takes to splice a four core multicore fiber to just 40 seconds, which is 4 times the length it takes to splice a standard single core fiber.
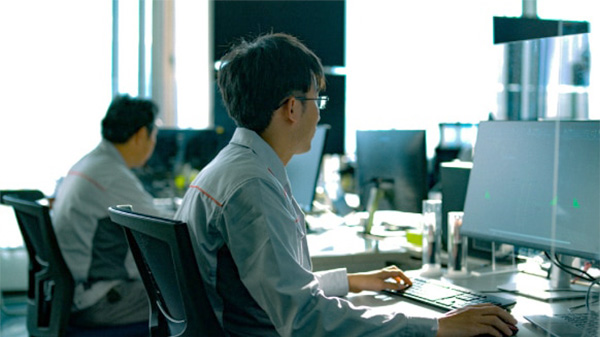
Creating the future of telecommunications infrastructure through new ideas and accumulated know-how
The fusion splicer realized higher performance while actively incorporating the ideas from young engineers, but the extensive use of the technology accumulated by Furukawa Electric is also one of the main features.
General-use fusion splicers apply voltage to heat the optical fiber placed between two discharge electrodes facing each other. However, Furukawa Electric’s fusion splicer surrounds and heats the optical fiber from three directions. This technology was originally used for splicing large-diameter optical fiber for optical fiber lasers, but it was applied to evenly heat multicore fiber, which has cores dispersed more toward the edges rather than the center.
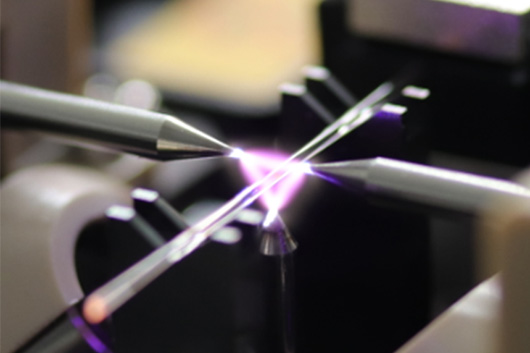
In this way, the fusion splicer developed through a combination of various technologies can be said to be the fruit of Furukawa Electric’s technology. Supporting this achievement is the long history of research and accumulated experience starting from the first appearance of optical fiber almost 50 years ago, as well as the mindset of actively taking on the challenge of developing new technology.
There is a special feeling of accomplishment when realizing the fruits of this labor by combining the accumulated knowledge and new ideas, and it further energizes the development workplace.
Development of multicore fiber itself has just begun within the industry, and the market for this product has great growth potential in the future. On the other hand, optical fiber is now widely used around the world and is increasingly becoming commodified. The same is true for fusion splicers. Given these trends, Furukawa Electric continues to place great importance on “providing high added value through the product and maximizing customer satisfaction”. Rather than focus only on price, by leveraging the high technological capabilities that are trusted by the customer, we will continue to take on new challenges and contribute to society.
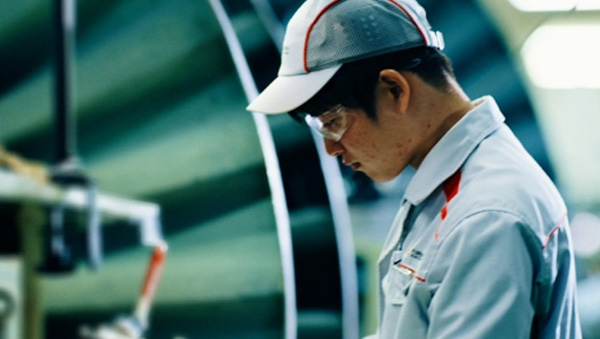