Aiming to achieve carbon neutrality in 2050. Furukawa AS’s aluminum wire and Alpha Terminal® are lightweight and utilize corrosion-proof technology
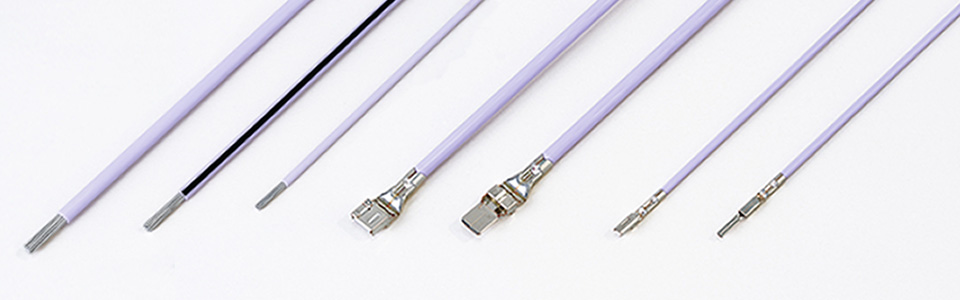
Automobiles have become an essential means of transportation in daily life. Recently, they are being equipped with various devices that support safe, secure and convenient mobility. On the other hand, directed at realizing a carbon neutral society, there are growing calls to decrease vehicle weight as a means of reducing CO2 emissions. In response, Furukawa AS, a member of the Furukawa Electric Group that develops and manufactures mainly car electronics, continues to challenge the development of technology for reducing the weight the wires used in automobiles.
※ Alpha Terminal® is a registered trademark of Furukawa Electric Co., Ltd. and Furukawa Automotive Systems Inc.
Furukawa AS aluminum wiring harnesses reduce vehicle weight and carbon emissions during manufacturing!
In recent years, automobiles have evolved in a number of ways, including the use of driver-assistance systems that reduce traffic accidents and implementation of autonomous driving technology that will resolve the shortage of drivers in the aging society. Also, with the introduction of EV (electric vehicles), vehicle weight tends to increase after equipping the large capacity batteries and other devices. In response, attention has turned toward reducing the weight of the wiring harnesses used to connect the installed batteries and electronic devices. Furukawa AS realizes reduced vehicle weight directed at realizing a carbon-free society through a conversion to aluminum for the wiring harnesses.
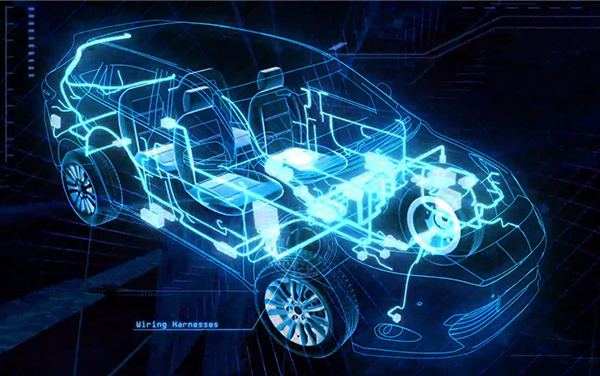
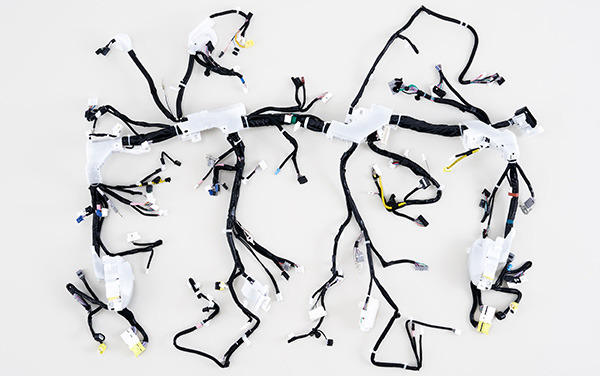
Traditionally, wiring harnesses use copper wire as the conductor, and they typically weight about 20kg in a passenger vehicle and about 50kg in a large SUV. On the other hand, using aluminum, which weighs 66% less than copper, as the conductor, it is possible to reduce wiring harness weight by over 10%.
Furukawa AS’s aluminum wiring harnesses combine aluminum and copper wire with copper terminals. In the manufacturing process, the aluminum is processed at an overseas factory using hydroelectric power, and the copper is processed at the Nikko Works using hydroelectric power and at the Mie Works using solar power. Also, geothermal power is used in addition to solar power for connecting the wire and terminal. In this way, thorough efforts are made to be environmentally friendly throughout the manufacturing process.
Key feature is “corrosion-proof” realized through proprietary welding technology
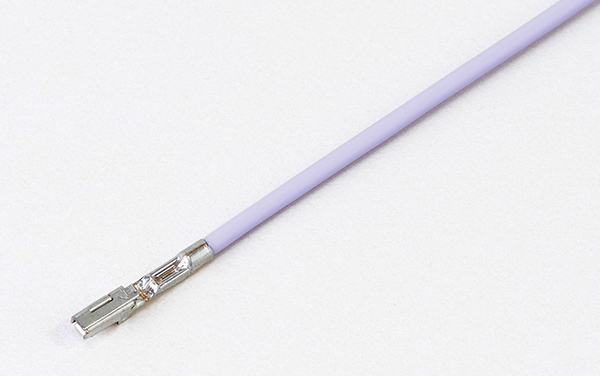
Actually, reducing weight by replacing the copper wires used in wiring harnesses with aluminum wires has been studied by various companies in the industry since the introduction of electric motors such as those for power windows. However, it is generally difficult to use aluminum for both the electrical wire and the terminals used for the connection to electronic. Therefore, the connection is made through different metals, “aluminum electric wire” and “copper terminals”.
The key point here is preventing corrosion of the metal. When water adheres to the point of contact between different metals, a chemical reaction called “contact corrosion of different metals” causes surface corrosion. Preventing this corrosion is a major issue.
In response, completely covering the aluminum and copper joint with plastic was considered as a way to prevent the infiltration of water. However, this would lengthen the wiring harness manufacturing process and lead to higher costs. As a result, shifting to aluminum wiring harnesses has been viewed to be difficult.
To solve this issue, Furukawa AS used welding technology to form the copper terminal into an airtight tubular shape. Then, by inserting the aluminum wire into the terminal and crimping to eliminate all open spaces, it was possible to realize corrosion-proof function without using plastic. The development project for this new Alpha Terminal® was launched in 2012.
However, as evidenced by the use for heat dispersion products, copper has extremely high thermal conductivity and easily disperses thermal energy. As a result, it is an extremely difficult metal to weld. Using welding technology for small terminals was a new challenge itself, so development was carried out while combining the knowledge and technology of the entire Furukawa Electric Group.
To date, Furukawa Electric Group has utilized the various advanced technology accumulated in the optical telecommunications domain (optical fiber, semiconductor lasers, optical fusion technology, etc.) to combine independently developed high precision 3D laser welding technology with an in-house manufactured fiber laser oscillator possessing high energy density through high light harvesting ability. The combination of these realized inline manufacturing technology for a high-speed press and fiber laser welding, leading to the successful development of the Alpha Terminal® that uses fiber laser welding to form the tubular shape and crimping to eliminate the open spaces between the copper terminal and aluminum wire.
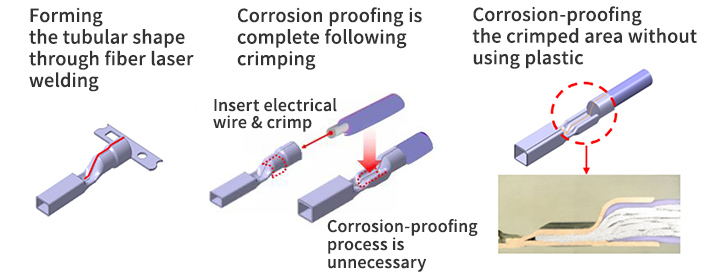
A stable mass production system for the Alpha Terminal® was established in 2015, and it is possible to manufacture several hundred terminals every minute. Even our customers were surprised by the precise, high-speed manufacturing technology.
Also, as more wiring harnesses are used following increased vehicle performance, there is higher risk of water coming into contact with the harness through condensation and consuming food and drink in the vehicle. Alpha Terminal® is unaffected even in these situations, leading customers to again recognize the extent of our corrosion-proofing technology.
Undertaking further challenges aimed at realizing carbon neutral automobiles
Automobiles are expected to further evolve. In particular, the Japanese government has announced the policy of “aim to realize carbon neutrality in the entire vehicle life cycle by 2050”, and the EV wave is expected to accelerate further in Japan.
Compared to ICE (internal combustion engine using gasoline or other fossil fuel) vehicles, EV are powered by an electric motor that uses electricity. Given this, EV motors need to be durable enough to withstand large flows of electricity, so it is necessary to use large (fat) wires to connect the high voltage battery and EV motor. However, fatter wires are larger, and the wiring harness loses flexibility, making it more difficult to route the harness within the vehicle.
In response to this, Furukawa AS has realized electrical wire with both heat resistance and flexibility through the use of Furukawa Electric Group’s polymer component technology. Through this, we are aiming to contribute to the increased use of EV and realization of carbon neutral vehicles.
In addition, we intend to address the issue of wiring harness recycling going forward. Today, wiring harnesses use various types of metal and plastic, and it is difficult to completely sort and recover all of these both in terms of technology and cost. The technology and system for recycling wiring harnesses still have not been established. Given this, we have set the immediate goal of creating technology that enables used wiring harnesses to be transformed into new wiring harnesses. We will further contribute to realizing carbon neutral vehicles in 2050.