Steadily working for 10 years with the aim of realizing a sustainable society. Story behind the development of the new biomass material CELRe
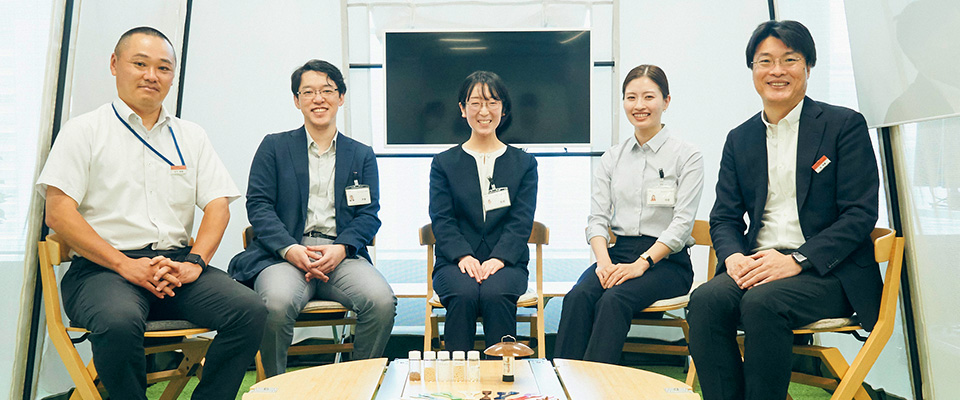
Following the global trend toward decarbonization and sustainability, the initiatives for developing products and materials with low environmental burden are a pressing issue. Furukawa Electric is also working to reduce greenhouse gas emissions in the entire value chain. Within these efforts, the Polymer Processing Technology Section in the Material Innovation Center at the Material Laboratory spent 10 years developing the new environmentally friendly material CELRe. We asked 5 members involved in the CELRe business about the development of this new material and the efforts toward contributing to co-creation and realizing a recycling-based society.
-
※
CELRe is a registered trademark of Furukawa Electric Co., Ltd. in Japan
-
- Yukihiro Ikura
- Manager of Polymer Processing Technology Section
As the team leader who oversaw the development team members involved in the development of CELRe, he sought to maintain active communication even during the COVID pandemic and create a workplace environment that facilitated discussions.
-
- Jaekyung Kim
- Polymer Processing Technology Section
As the person responsible for developing the manufacturing process for CELRe, he was a driving force within the team since the start of development.
-
- Yui Hamuro
- Polymer Processing Technology Section
From the first year of joining the company, she worked to develop processing technology for cellulose and rubber.
-
- Mayu Satake
- Polymer Processing Technology Section
From the first year of joining the company, she conducted research aimed at increasing the strength of cellulose.
-
- Hiroki Kinoshita
- Polymer Processing Technology Section
The person responsible for overall testing, processing and manufacturing of CELRe. He was the person to give CELRe its name.
Contributing to the next-generation society! The new biomass material CELRe
- First, what kind of material is CELRe?
Ikura: It is “cellulose fiber reinforced plastic” made by mixing plant-based cellulose fibers with resin. Directed at realizing a sustainable society, reducing the amount of plastic used is a major issue. As the legal framework for recycling becomes better defined, now is the time for manufacturers such as us to develop actual products that will lead to carbon neutrality. CELRe is one of the products that have been developed.
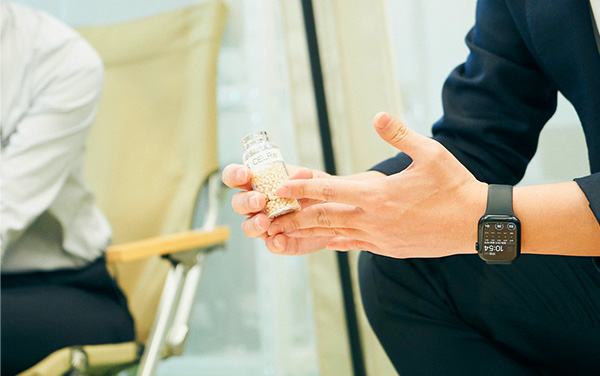
Hamuro: One of the main features of CELRe is that the content of plant-based resin has been increased from around 20% in normal materials to at least 51% while maintaining the product strength. The excellent recyclability will lead to increased product life, and as a result, it will contribute to reducing CO₂ emissions.
Satake: he fact that CELRe utilizes polymer technology unique to us as a power cable manufacturer is also one of the features. It can be said that CELRe was born through a combination of the company’s technology accumulated over the past 50 years and newly developed technology.
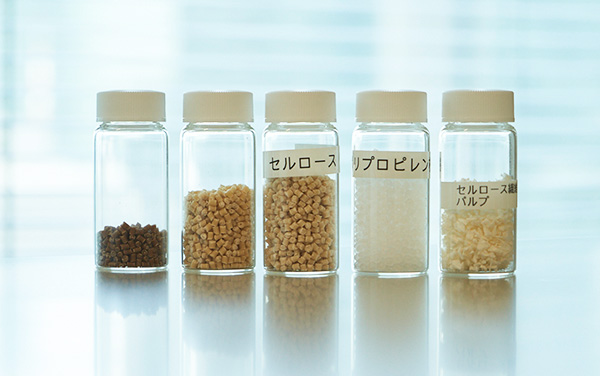
Kim: It looks basically the same as traditional plastic. The material itself has a pale brown color, so it is easy to create various colors by adding a colorant. As an example from daily life, it can be used for outdoor products, such as those used when camping.
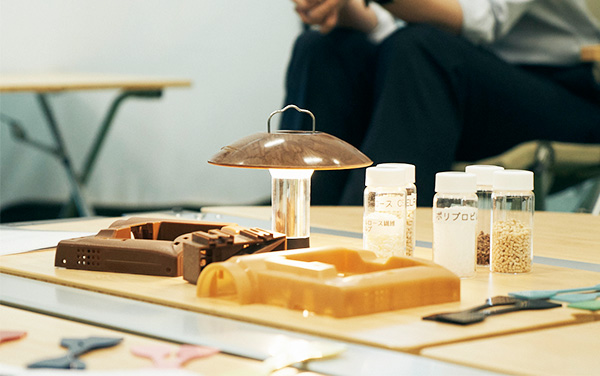
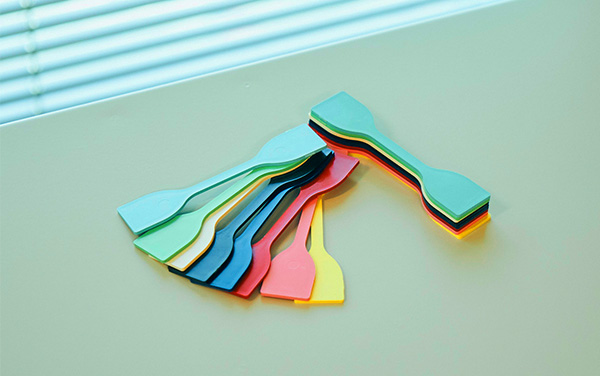
Kinoshita: As the origin of the name CELRe, “CEL” comes from cellulose and “Re” comes from resin, reinforcement and recycle, so the name incorporates a number of meanings. In the current project, we were allowed to name the new product, and my proposed name “CELRe” was selected.
Repeated trial and error. Why did the team continue to single-mindedly undertake this challenge?
- When did the development of CELRe begin? Also, during development, what were some of the “challenges” you faced?
Kim: The development project began in 2014. Initially, we only expected it to last around 3 years, but this year will be the 10th year. Rarely does the company spend such a long time developing a new material. Despite the high expectations, development did not progress as smoothly as we had hoped, and we almost gave up at one point.
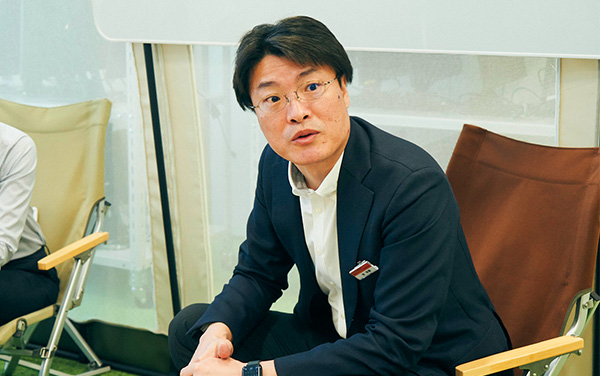
Ikura: Roughly speaking, the first 5 years were spent developing basic technology, and the following 2 years were spent establishing a system for mass production. Efforts during the final 2-3 years were focused on conducting PR to customers. Each phase involved its own various challenges.
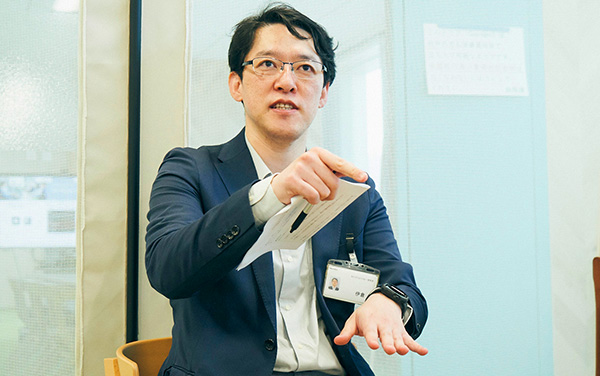
Hamuro: Mainly Satake-san and I were involved in developing the material. I researched processing technology for combining cellulose and rubber. Basically, cellulose and rubber are similar to water and oil, meaning they are difficult to mix together. I needed to investigate what additives are required to make these opposing materials stick together.
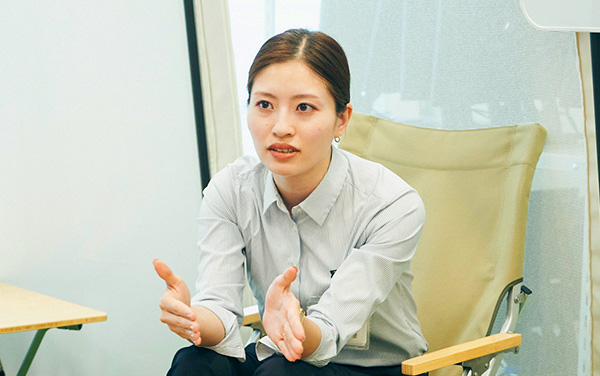
Ikura: Nobody on the team possessed thorough knowledge of the field you were researching, so it must have been difficult.
Hamuro: That’s true. I was assigned this job just after graduating, and at first, I had a positive attitude and wanted to try everything. However, as my research progressed, I started to realize my situation and the major obstacles I faced. I wondered if I could actually realize any results.
The materials we handled up to now have been synthetic, and it is difficult to control natural materials like cellulose. There were times when the same test would produce different results the next day. I moved forward with my analysis while receiving assistance from other departments.
Satake: My job was to increase the strength of CELRe while maintaining the reliability as a material. Since joining the company, I have researched how to maintain the characteristics of CELRe after it absorbs water, but my first year of research was terrible.
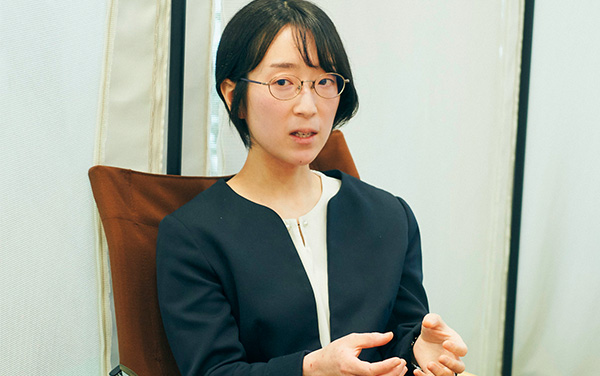
The changes to a material’s characteristics after it absorbs water are investigated in a device called a damp heat tester, but it takes about a month and a half until the results are available. Sometimes, I would conduct the test after performing various investigations only to learn a month and a half later that the strength had decreased. Such moments were disappointing, but there was no quitting. I would think about what improvements to make and conduct the test again. My days were spent in repeated trial and error.
Kim: In many cases, the good ways to make cellulose and resin stick together have already been patented. Given this, Satake-san had to work from scratch to find a way. It involved investigating the characteristics of materials that exist in the natural world and using them in a way nobody ever has before. I think it was quite a feat.
Satake: I was discouraged when I could not determine the root cause of the problem I was facing, but I read a large volume of literature, participated in academic conferences and repeatedly set and validated hypotheses focusing on the mechanism of the material. I inspired myself to do whatever it took to achieve results, and I unconsciously made a gesture of triumph with my fist when I was ultimately successful.
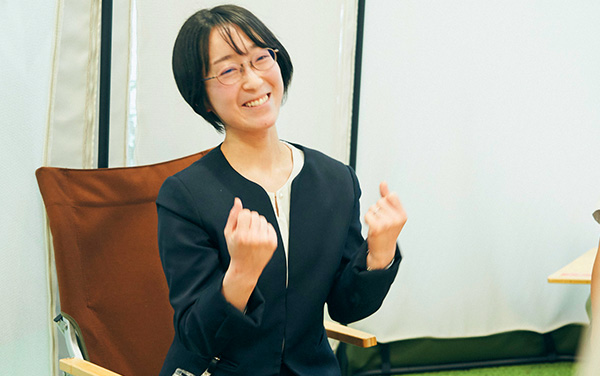
Kinoshita: My role was to mass produce the material developed by Hamuro-san and Satake-san. In order to use CELRe for actual products, it was essential to establish a stable, efficient mass production system that used extruders to form the material. However, this process also involved one challenge after another. Many times, although the laboratory test was a success, it would fail during the continuous production process in the actual workplace using extruders.
In addition, this work was carried out during the first wave of the COVID-19 virus. While there were still many unknowns about the virus, the restrictions on coming to the office and working from home increased, and it was difficult to receive the supply of materials. This was truly a challenging time to conduct experiments.
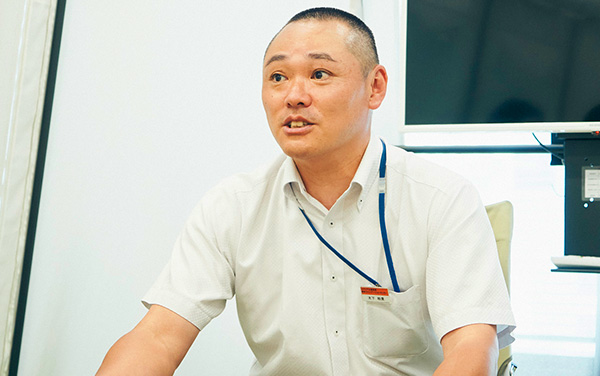
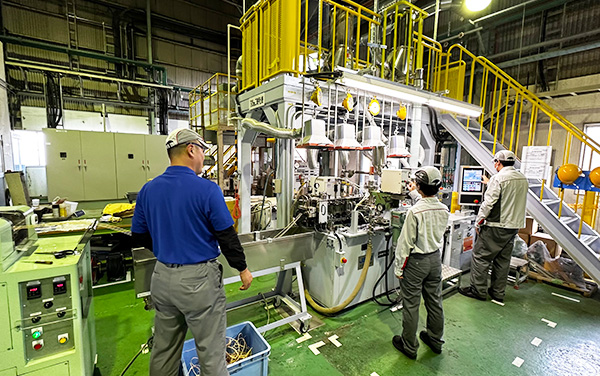
Ikura: Before, everyone would gather around the machinery and conduct experiments while holding discussions, and sometimes, a vendor would be called in to handle an issue. However, this was difficult to do during the COVID pandemic. In online meetings, the team members had to focus on the workplace images shown on the computer and try to confirm based on what they could see on the screen.
Kinoshita: We finally saw the light at the end of the tunnel around the end of 2022, and the mass production system was prepared in January and February the following year. The progress was not always smooth, but we steadily moved forward one step at a time without rushing. I believe this enabled us to make improvements to the problems we encountered. Once the name CELRe was selected, I felt a sense of responsibility that prohibited me from giving up.
Hamuro: Speaking of responsibility, I am grateful to have been given the freedom to basically carry out the work in my designated area on my own. It was easy to consult with the others around me, so I also never felt isolated.
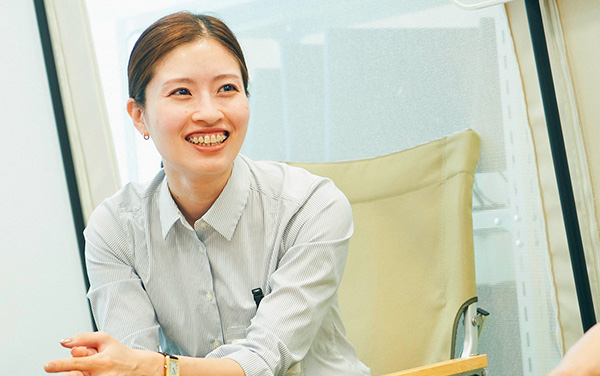
Satake: Definitely, we were given a great deal of freedom in this project. I think the reason the work was fun despite all of the difficult challenges was the fact that we were given so much freedom. When reporting the results of the experiments, our knowledgeable superiors quickly provided feedback, and I was able to move forward while incorporating perspectives other than my own.
Ikura: Due to the impact of COVID, it was not possible to have passing conversations, so I had to intentionally initiate communication, such as through the use of chat tools. In order to enable everyone to comfortably carry out their work, I aimed to quickly provide the first reaction as the person responsible for overseeing the project.
Kim: Receiving any kind of reaction makes it easier to take the next action. Also, it is definitely important to return to the starting point when running into a wall. I don’t think it is necessary to do anything special. While steadily implementing the PDCA cycle, continue to tenaciously act without giving up. I believe this is what we did, and our ability to do this led to the current result.
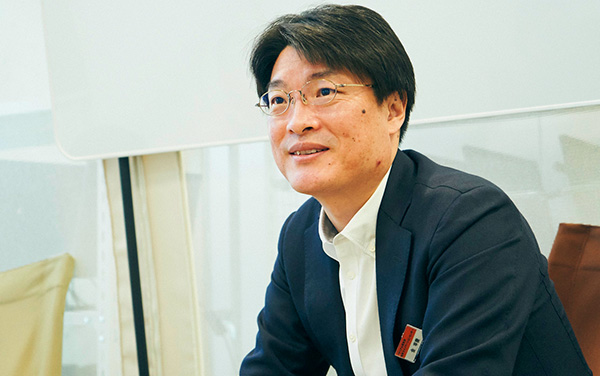
Aiming to realize a sustainable future that uses CELRe in everyday products
- What are your hopes for CELRe in the future, and what issues do you foresee?
Kinoshita: First, because simply using CELRe will reduce the burden on the environment, I believe searching for applications to enable as many people as possible to use CELRe is the issue now.
Our current customers are mainly household appliance and office furniture manufacturers, but leveraging the material’s high strength and reliability, it is planned to use CELRe for automobile products. On the other hand, it costs money for a customer to switch to a new material from a material they have a lot of experience with, and there are also psychological barriers. It will be important for us to tear down these barriers.
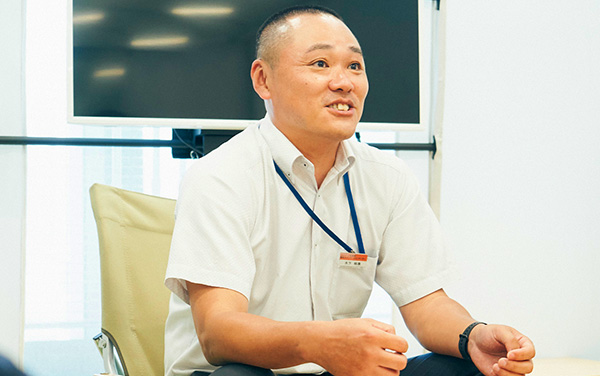
Hamuro: Increasing awareness of CELRe is important. If we can do this, new ideas such as “Can I use it for this product?” may be generated by the customer. Creating such a cycle is ideal, and I want CELRe to be adopted for products that are used in everyday life by the average person.
Kim: In order to realize a sustainable society, I think it will be important for each and every person to personalize the issue. Making CELRe a more common presence in daily life will hopefully provide an opportunity for more people to think about how the sustainable society should be organized.
Satake: I want to increase the ratio of plant-based resin from the current 51% to 100%. I believe this is the ultimate goal for CELRe, and it is the challenge we should strive to achieve.
Ikura: Furukawa Electric values “searching for and deepening technology”. R&D members often tend to focus on “deepening” technology, but “searching”, which involves interacting with the outside and having a broad perspective, is equally important. Through the CELRe project, I was able to experience this once again. Going forward, while balancing between “deepening” and “searching”, I want to contribute to creating an even better society.
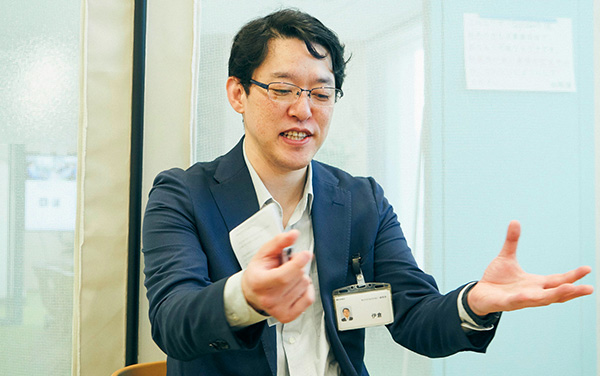
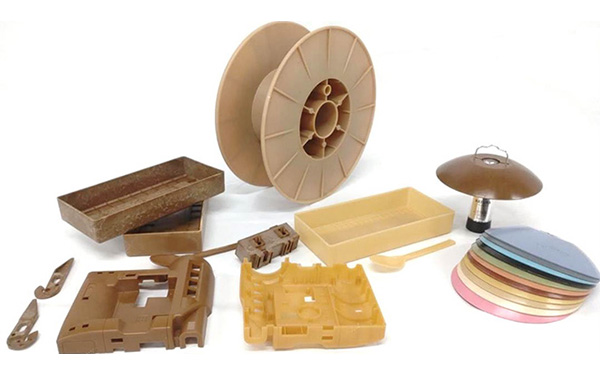