Advanced recycling technology has been realized overseas! Story behind starting production of “GREEN TROUGH®” made from 100% recycled plastic in Europe
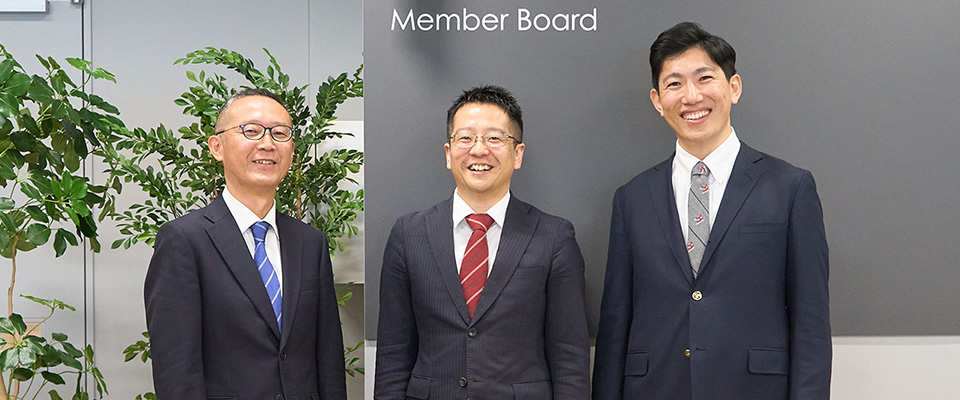
The plastic material used in the Green Trough® cable trough manufactured and selling by Furukawa Electric is 100% recycled plastic since 2003. This environmentally-friendly product has also been well received overseas mainly in Europe, and starting from expanding to the UK in 2013, Green Trough® has also been introduced in countries including Germany and Denmark.
As the next phase, “local production” began in Europe from July 2023. Pride in the technology and diligent communication led to the success of this next step. We talked to 3 central project members about the story leading up to the start of production overseas and their future goals.
- *Green Trough is a registered trademark of Furukawa Electric Co.,Ltd. in Japan
-
- Satoshi Kozawa
- General Manager of Innovative Products Development Project Team, AT & Functional Plastics Division
Oversaw the technology related matters in the Green Trough® Project. He has been a member since the start of overseas sales in 2013.
-
- Hirotaka Okada
- Global Business Development Department, AT & Functional Plastics Division (Assigned to Trocellen GmbH)
Green Trough® Project Leader. As the marketing representative, he is working to increase sales and expand the market in Europe.
-
- Takashi Hori
- Manager of Overseas Engineering section, Innovative Products Development Project Team, AT & Functional Plastics Division
Local manufacturing manager responsible for the manufacturing process and technical matters. He is also providing technical support for products overseas other than Green Trough®.
Recycling 5,000 tons of plastic every year into an appealing product
— First, tell me about Green Trough®. What are its features and strengths, and how is it used?
Kozawa: Green Trough® is a cable trough made from recycled plastic. Cable troughs are mainly used to protect and house the cables installed for communications, signal transmission and electric power for railroads and roads.
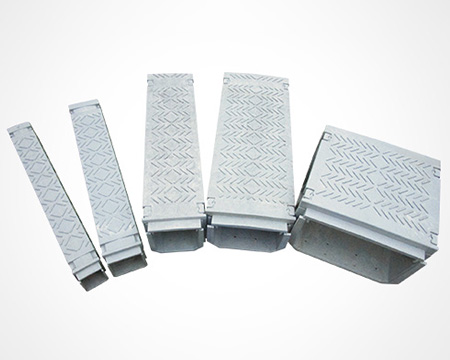
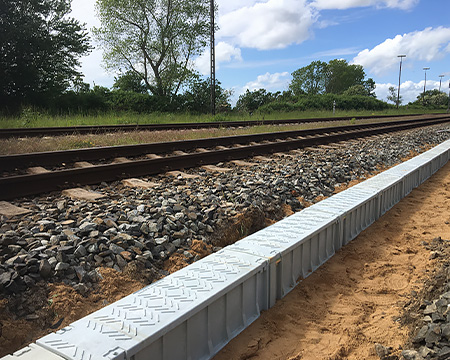
Generally, cable troughs have been made of concrete, but there are issues in terms of work efficiency and worker safety. It is only possible to install several dozen up to several hundred troughs per day. Concrete troughs weigh between 50-100kg each, so they need to be transported by heavy machinery. This limits the number that can be installed each day.
On the other hand, Green Trough® is made from recycled plastic and extremely lightweight. Weighing 75% less than concrete troughs, Green Trough® is easy to carry and can be moved by hand. In addition to being environmentally friendly, it is possible to reduce man-hours and also increase worker safety. Given these features, Green Trough® has been held in extremely high regard since first being launched 20 years ago.
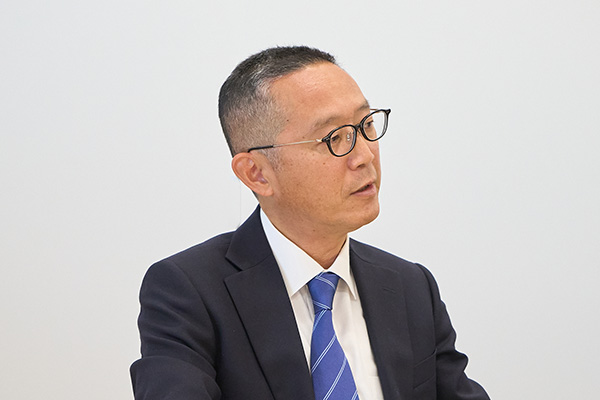
— I understand they are made from recycled plastic, but specifically, what kind of plastic is used?
Hori: The plastic containers and bags we commonly throw away everyday become the raw material, and we use about 5,000 tons in Japan and overseas combined every year. Recycled plastic is difficult to process due to the various types of plastic contained and degradation, and there are issues in terms of strength and durability. At Furukawa Electric, we utilize our unique additive technology to create extremely strong, durable cable troughs.
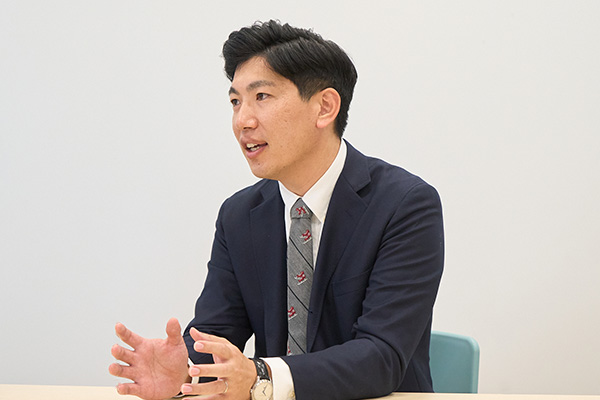
COVID-19, invasion of Ukraine… The impact of world events made exporting more difficult
— Following launch in Japan in 2003, I understand that sales of Green Trough® were expanded to Europe in 2013.
Okada: Initially, sales overseas began in the UK. Japanese trains run on electricity, but many of the trains in the UK at the time were powered by diesel, and there was increasing movement toward quick electrification of these trains. Within this trend, Green Trough® received increased attention for their lightweight and the ability to install twice as fast compared to existing concrete troughs, and this led to the adoption of our cable troughs.
At the same time, increased environmental awareness in Europe was also a major factor behind the expansion of Green Trough® overseas. When talking to local customers overseas, awareness of protecting the environment existed not only within executive management but also among the site managers. In addition to material related inquiries, I often received detailed inquiries about CO2 emissions during transportation and the source of electricity used in manufacturing. This awareness has enabled customers to feel the appeal of our Green Trough® made from recycled plastic.
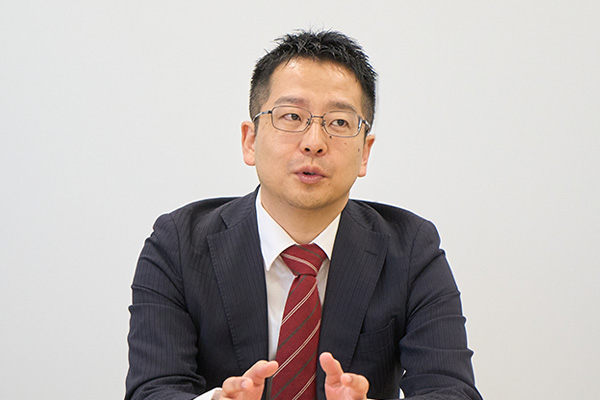
— Am I correct that at the time, the products were exported from Japan?
Kozawa: That is correct. They were shipped from Japan by sea in a voyage that took 6 weeks to reach Europe. However, the spread of COVID-19 caused a shipping crisis. Logistics were disrupted, and costs exploded. Given the untenable position, we started considering local production.
Okada: COVID-19 made it difficult to secure transportation containers. Frequently, we were able to make a reservation and formulate a shipping schedule only to have the reservation cancelled the following day. In addition, the grounding of a containership in the Suez Canal in 2021 impeded normal ship traffic. As a result, we considered starting transportation on the Siberian railroad, but the invasion of Ukraine by Russia stopped this means of transportation, too. Having all the modes of transportation cut off was a major turning point.
Hori: The increased market potential of Europe was also a major factor behind deciding to steer toward local production. EU (European Union) set forth the goal of becoming the world’s first “climate neutral* continent” by 2050 and announced the European Green Deal for fundamentally revising the energy, food and transportation systems in Europe. In order to realize this, a shift has begun away from automobiles toward railroads as the means of transportation, and the railroad market is becoming more active. We felt this was a good opportunity to enter the market.
- *Climate neutral: Environmental protection initiative that aims to achieve substantially zero (net zero) greenhouse gas emissions from the daily life and manufacturing activities of people, companies and organizations.
Okada: Using European recycled plastic materials as the raw material will contribute to improving the local environmental problems, and eliminating the need to transport product from Japan will also reduce CO2 emissions from transportation. The belief that we can achieve a strong presence in Europe, too, by highlighting these appealing aspects led to the start of a project in 2021 aimed at realizing local production.
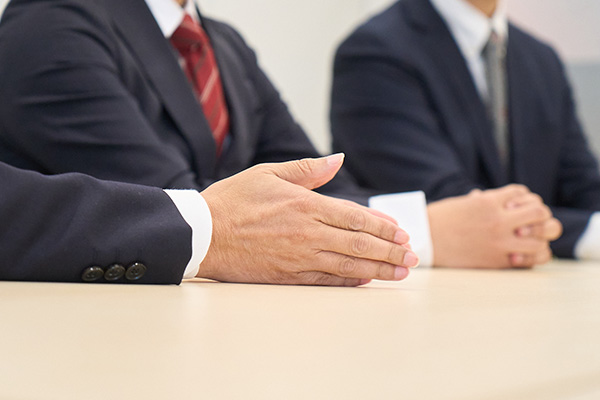
Procuring materials and searching for a production site in partnership with the local members
— What were the first steps taken toward starting local production?
Hori: We started searching for a local production site and material suppliers. It goes without saying, but it is impossible to manufacture anything without raw materials. However, we hit a roadblock when we were unable to find materials with suitable characteristics at the right price. We sought assistance from the group company Trocellen based in Germany, and we diligently searched for suppliers and OEM manufacturers by attending exhibitions and individually visiting every company found on the Internet.
Okada: As project leader, I assisted in terms of sales. In order to expand local production in the future, there needs to be a market. Our group company Furukawa Electric Europe Ltd. (FEEL) based in the UK handles sales for the EU, and I have continued to share this need to grow the market with the members of FEEL. In relation to this, we acquired product certification from a German railroad company in 2021 and successfully secured a multi-year annual contract from a Danish railroad company. The future outlook is starting to become brighter, but we still have much work to do. Concrete troughs are still the main product, and continuing to thoroughly convey the merits of using Green Trough® will be key to expanding the market.
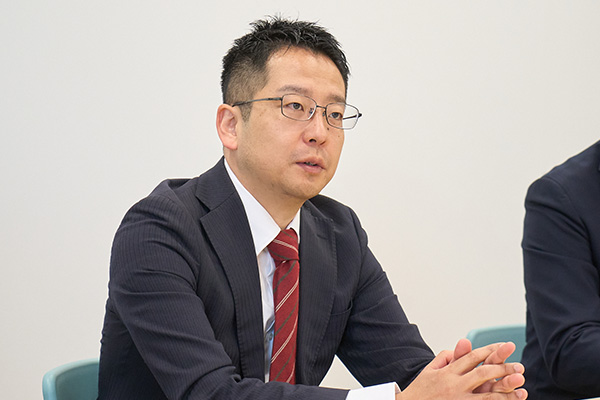
— Was the project carried out in partnership with a number of local companies, including Trocellen, FEEL and the local manufacturers (OEM)?
Okada: Yes. Given the need to realize local production as quickly as possible, this “speed” was extremely important to the project. When working with the heads of each division and president of Trocellen, I received great assistance in many areas, including the formation of a strong local project team, gathering information, quickly providing meticulous reports and advice about expanding into the local area. I believe this assistance enabled us to move forward.
Hori: COVID-19 prevented us from freely traveling to Europe, but I am grateful for the proactive communication with our colleagues overseas, including the independent creation of shared tools.
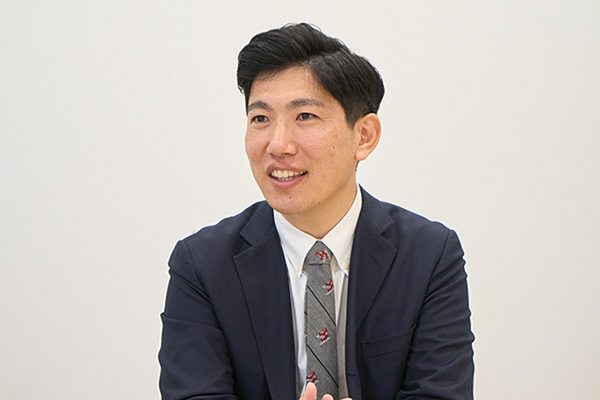
Realizing “Furukawa Electric quality” through communication between dedicated professionals
— Where did you focus your efforts in order to make local production in Europe a success?
Okada: When working with FEEL to acquire new orders, I focused on thoroughly and repeatedly conveying our intended message to the customer. The representatives explain the product to customers in English, German and Danish, but it is difficult to fully understand the appeal of Green Trough® without translating the detailed nuance of the original Japanese. Therefore, I repeatedly conveyed the product features and appeal to the point of being annoying.
Hori: Manufacturing faced a similar experience. When manufacturing in Europe, we want to create products with the desired quality, so it was necessary to explain each process in detail and then repeat it again if the process was carried out correctly… At the beginning, I was often told, “Furukawa Electric requires everything to be 100%” and “It is so detailed”, but I don’t think this was meant in a negative sense. As time went on, the local members took on a more positive attitude of, “If we give this much attention to detail, we will be able to make excellent products”, and I was happy to see them engage in the work based on agreement with the requirements.
Kozawa: I noticed the local production members becoming more actively engaged every day. They created standards based on personally prepared memos and pictures, as well as made constructive proposals and understood the required level. I feel we were able to share our passion toward monozukuri and as engineers despite the language barriers.
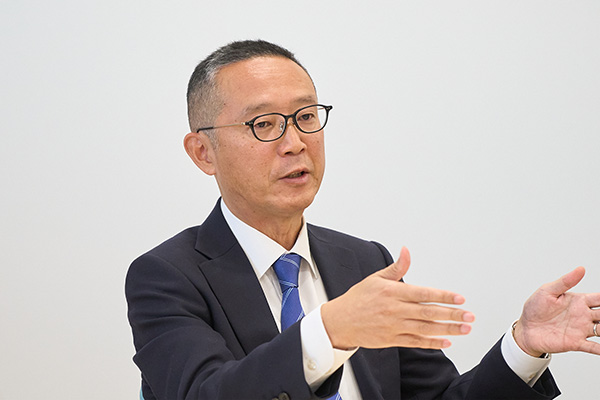
Hori: From the perspective of product reliability, we acquired “Environmental Product Declaration (EPD)” with an eye toward growing the market in the future. EPD is third party certification based on quantification of a product’s impact on the environment from selection of the resources and materials through to delivery to the customer. In recent years, CO2 emissions from construction worksites are being checked more strictly particularly in Europe, and we are often asked during the bidding stage whether we have acquired EPD. In fact, we were required to present EPD certification when submitting a bid in Australia and acquired the order because we had received EPD certification.
Improving the technology and contributing to global infrastructure from the standpoint of environmental protection
— Your hard work led to the start of local production in July 2023. Looking back, what are your honest thoughts about the project?
Okada: My impression was “awareness rubs off”. After it became difficult to export from Japan, our mission became the rapid start of local production. Honestly, I occasionally woke up in the morning hoping everything was resolved, but I decided that hope will not change anything and we must do it ourselves. Along with this sincere determination, the issues being faced, the importance of the project and the need to proceed quickly were thoroughly conveyed to the department members and local members, and I believe it was possible to achieve success by bringing everyone together around the same awareness.
Hori: I was simply filled with joy when the first product was completed at the local factory. It was the result of diligent communication and orienting everyone toward the same goal of wanting to create good products.
From the right, Mr. Andreas Hagedorn of Trocellen, Mr. Francesco Scarano of Trocellen and Mr. Aleksander of an affiliate company
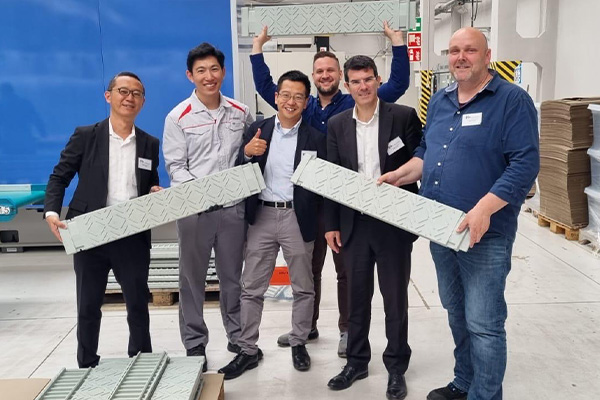
— What are your thoughts about the future of the business?
Hori: Some of the additives used in manufacturing are still exported from Japan, so my short-term goal is to realize 100% local procurement. This will eliminate the CO2 emissions from maritime shipping, and if we can realize this, it will lead to our products being held in even higher regard by customers.
Kozawa: When talking to a company in the UK, I was told, “I want a product that is Anti slip because we walk on top of the troughs”. We actually made product that responded to those needs. This made me realize that although walking on the troughs is generally prohibited in Japan from the perspective of safety, different countries have different rules. Each country likely has different needs such as this example, so after holding hearings with the customers, I want to create localized products that suit the needs of each country.
Okada: Furukawa Electric has contributed to building infrastructure in Japan and overseas. Without limiting to just Green Trough®, I believe it is our mission to develop products that use recycled materials and expand the business in a way that matches the market needs. Creating the next idea, next product and next market is the role we need to fulfill.
Kozawa: That’s true. We are currently working to develop various recycling technology, with aim of using 100% recycled materials in the manufacture of our division’s other major products EFLEX (Protective tube used for installing underground cables) and EFCELL (Non-crosslinked low-expanded polypropylene sheet used for office files cover sheets, dividers, etc.). We are aiming to contribute to the realization of a truly prosperous, sustainable society. We will continue to improve the technology and contribute to solving environmentally issues around the world.
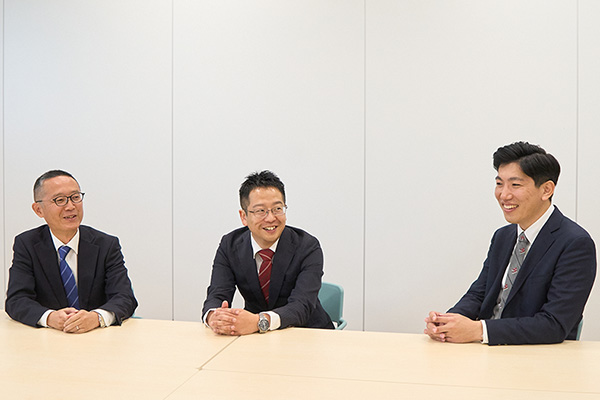