サステナブルな社会を目指して、着実に挑み続けた10年間。バイオマス新素材「CELRe®」開発ストーリー
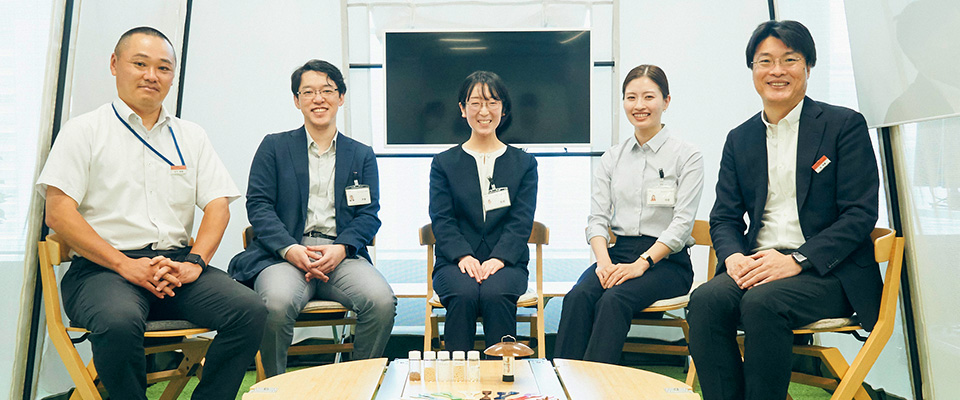
世界的な脱炭素化やサステナブル化の潮流に伴い、環境負荷の少ない製品・素材の開発に向けた取り組みは喫緊の課題。古河電工も、バリューチェーン全体での温室効果ガス削減に取り組んでいます。そんな中、マテリアル研究所素材力イノベーションセンターポリマー技術開発課は環境配慮型の新素材「CELRe®(セルレ)」を足掛け10年で開発しました。共創・循環型社会の実現に貢献するべく奮闘した日々とは? CELRe®事業に携わる5人のメンバーに、開発ストーリーを聞きました。
-
※
CELReは日本における古河電気工業株式会社の登録商標です
-
- いくら ゆきひろ 伊倉 幸広
-
ポリマー技術開発課長
2009年入社
開発メンバーをまとめるCELRe®開発チームのリーダー。コロナ禍でもコミュニケーションを活発に、相談しやすい環境づくりを意識。
-
- きむ ぜぎょん 金 宰慶
-
ポリマー技術開発課
2009年入社
CELRe®の製造プロセス開発を担当。開発当初からチームをけん引。
-
- はむろ ゆい 羽室 優衣
-
ポリマー技術開発課
2019年入社
入社1年目から、セルロースとゴムの加工技術の開発に挑戦。
-
- さたけ まゆ 佐武 真有
-
ポリマー技術開発課
2018年入社
入社1年目から、セルロースの強度向上達成に向けた研究に挑戦。
-
- きのした ひろき 木下 裕貴
-
ポリマー技術開発課
1994年入社
CELRe®の全般的な実験・加工・製造を担当。CELRe®の名付け親。
次世代の社会に貢献!注目のバイオマス新素材「CELRe®」
—はじめに、今回開発した「CELRe®」とはどのような素材なのでしょうか?
伊倉「植物由来のセルロース繊維と樹脂を混ぜ合わせて作った『セルロース繊維強化樹脂』です。昨今、持続可能な社会の実現に向けてプラスチックの使用量を削減していくことが大きな課題となっています。リサイクルなどに関する法律上の枠組みが整備されていく中、私たちメーカーはカーボンニュートラルにつながる実際の製品開発を進めている段階。そうして開発された製品の一つがCELRe®です」
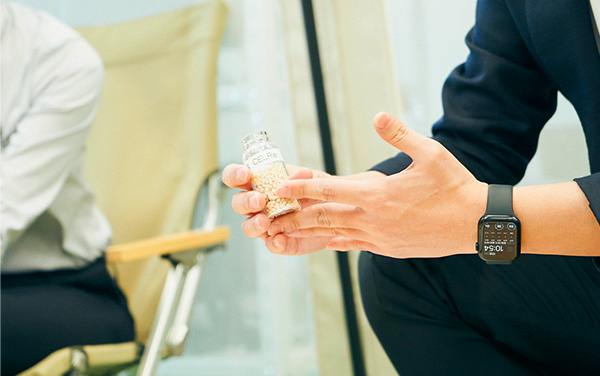
羽室「CELRe®の大きな特徴として、通常の素材では20%程度含まれている植物由来の樹脂が、製品としての強度を維持しながら51%以上含まれていることが挙げられます。リサイクル性に優れているので製品の寿命延長につながり、結果としてCO2排出量削減にも貢献しています」
佐武「電線メーカーならではのポリマー技術を活用していることも特徴の一つです。CELRe®は、当社が50年以上かけて培ってきた確固たる技術と、新たに開発した技術を掛け合わせて誕生した製品であると言えますね」
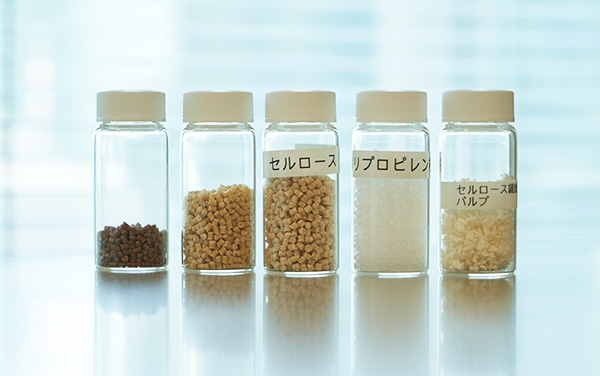
金「見た目は従来のプラスチックとほとんど同じ。素材そのものは淡い褐色のため、さまざまな色に染めやすいという特徴もあります。一例ですが、私たちの身近なところだとキャンプなどのアウトドア製品にも活用できると考えています」
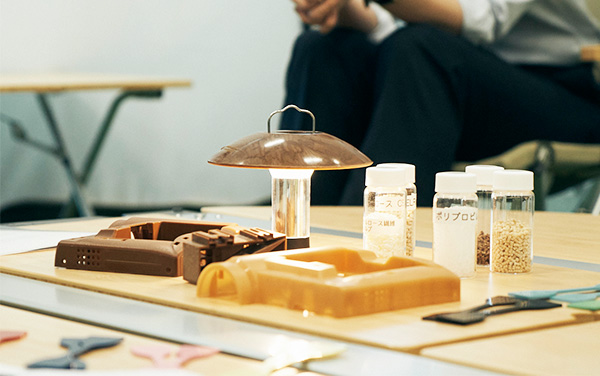
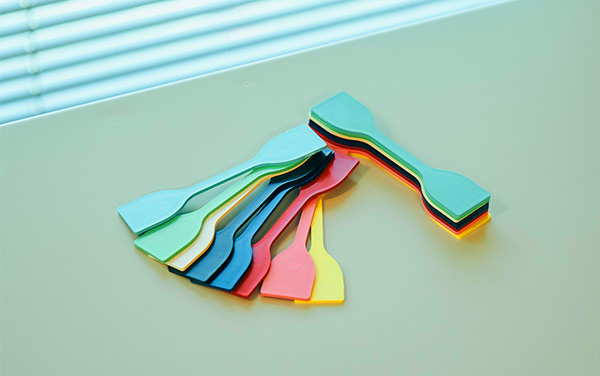
木下「CELRe®という名前は造語で、『CEL』はCellulose(セルロース)、『Re』にはResin(樹脂)、Reinforcement(強化)、Recycle(リサイクル)など、いろいろな意味が込められています。今回のプロジェクトでは製品名を検討するところから任せていただき、私が提案したCELRe®が採用されました」
試行錯誤を重ねた日々。ひたむきに挑戦し続けられた理由とは?
—CELRe®の開発プロジェクトはいつから開始したのでしょうか?また開発中、みなさんにとって“挑戦”だったことを教えてください。
金「スタートは2014年です。最初は3年程度で目処がつくと思っていましたが、今年で10年目。新素材の開発にこれだけ時間がかかるのは当社としてもめずらしいことです。周囲からの期待が高い一方、開発が思うように進まず、絶望しかけたときもありました」
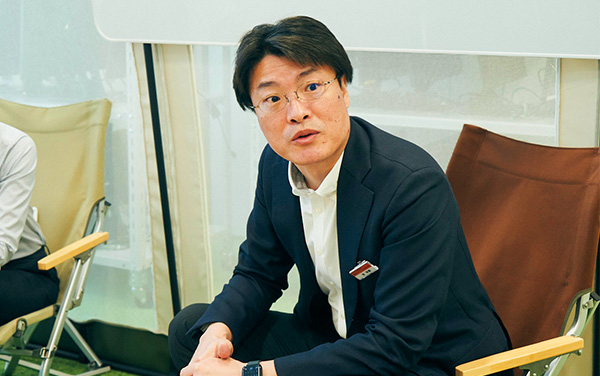
伊倉「ざっくりですが、10年のうち最初の5年間は基礎技術の開発期間、その後の2年間が製品として量産体制を構築することに費やした期間、そしてここ2、3年がお客さまへのPRに力を入れている期間です。どのフェーズにもさまざまな苦労がありました」
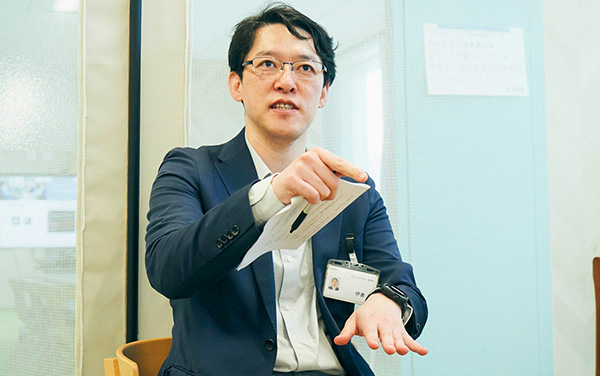
羽室「素材開発に主に関わったのは私と佐武さんで、私はセルロースとゴムを複合するための加工技術を研究していました。そもそもセルロースとゴムは水と油のような関係なので練ること自体が難しくて。相反するものをくっつけるために必要な添加物は何かを調べる必要がありました」
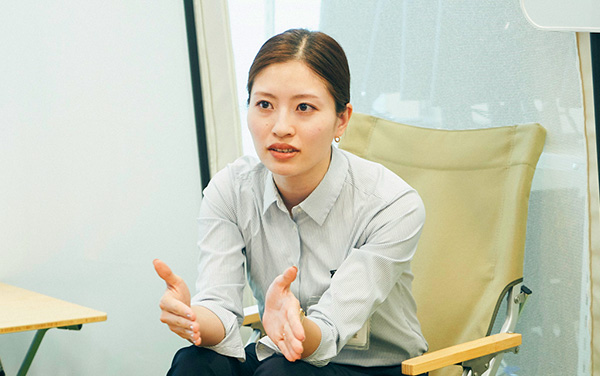
伊倉「羽室さんが研究している分野に詳しい人がチーム内にいなかったので大変でしたよね」
羽室「そうですね。私は新卒からこの仕事を任せていただいて、最初はできることはなんでもやってみようと前向きでした。ですが、研究を進めていくうちに自分の置かれている状況やハードルの高さに気づきはじめて、本当に実現できるのだろうか……と思いました。
私たちが今まで扱っていた素材は人工物でしたが、セルロースは天然物なのでコントロールもしづらいです。昨日と今日で同じ実験をしても違う結果が出ることもある。他の部門にも協力してもらいながら解析を進めていました」
佐武「私に任せられた仕事は、素材としての信頼性を保ちながらCELRe®の強度をいかにアップさせるか、でした。入社以来、水を吸った後もCELRe®の特性を維持するにはどうすべきかをずっと研究してきましたが、1年目は全くうまくいかなかったです。
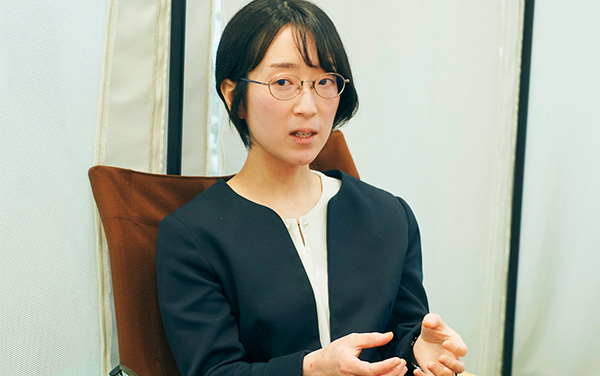
水を吸ったときの素材の特性の変化は湿熱試験機という機械で調べるのですが、結果が出るのに1か月半ほどかかるんです。いろいろ調べて、実験して、1か月半待ってやっと取り出してみたら強度が下がっていることも。その瞬間はがっかりしましたが、やめるわけにはいかないので、そこからどう改善するかを考えて、また実験して……。とにかく試行錯誤の日々でした」
金「セルロースと樹脂をくっつけるのによさそうな手法は、すでに特許が取られていることが多いんですよね。だから、佐武さんはゼロから見つけなければならなかった。自然界に存在する素材の特性を調べて、まだ世の中に知られていない、誰も用いていないやり方を見つけた。すごいことだと思います」
佐武「うまくいかない原因がわからないときは心が折れそうにもなりましたが、いろいろな文献を読んだり、学会に参加したりと、素材のメカニズムに着目して仮説検証を繰り返しました。やってやるぞという気持ちで自分を奮い立たせて、ついに成功したときは思わずガッツポーズが出ました」
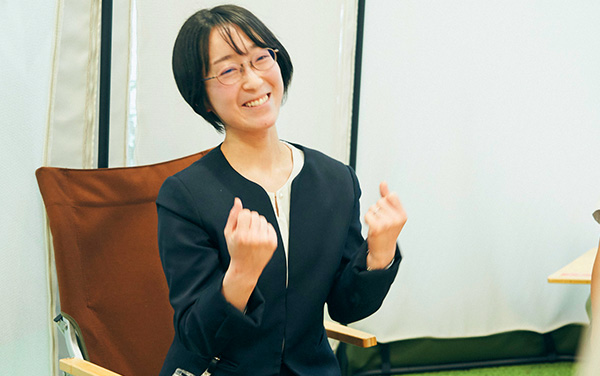
木下「私の役割は、羽室さんと佐武さんが開発した素材を量産することでした。CELRe®を実際の製品に使用するには、成形を行う押出機を使用した安定的・効率的な量産体制の構築が不可欠です。しかし、それもまた苦戦の連続。ラボでの実験では成功したけれど、押出機を使用した実際の現場における連続的なプロセスでは失敗する、ということが多かったです。
さらに、当時はコロナウイルス第一波の真っ只中。何が起きているかもよくわからないまま出社制限や在宅勤務が増えて、材料もなかなか供給されない。その中で実験を進めていくのは本当に大変でしたね」
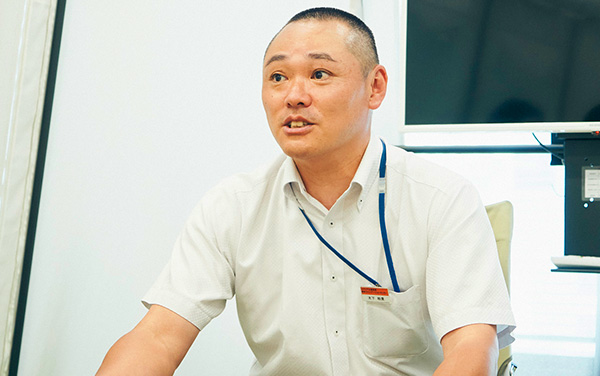
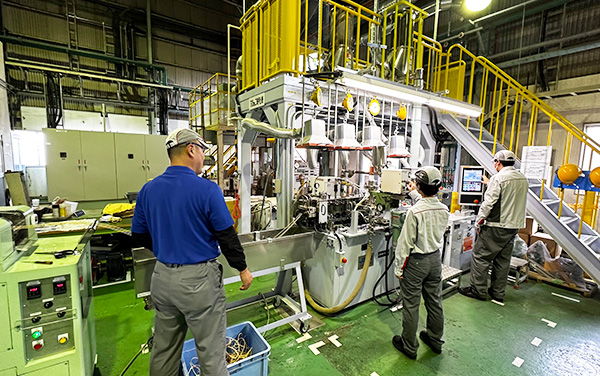
伊倉「以前はみんなで機械の前に集まって議論しながら実験したり、何かあった時に業者の方を呼んだりすることもできましたが、コロナ禍ではそれも難しく……。オンライン会議で、メンバーがパソコンで映してくれた現場の様子を、画面越しに目を凝らして確認していました」
木下「目処がついたのは2022年の年末くらい。年明けの1、2月あたりで量産体制が整いましたね。順調に進まなかったので時間はかかりましたが、焦らず一歩ずつ前に進む。そうすることで問題点を改善していけたのだと思います。CELRe®という名前を採用してもらった手前、諦めるわけにはいかないなと、責任感もありました」
羽室「責任で言うと、私は基本的に自分の担当領域を自由に任せてもらえていたことがありがたかったです。周りの方に相談しやすい環境だったので、一人で抱えることもなかったですね」
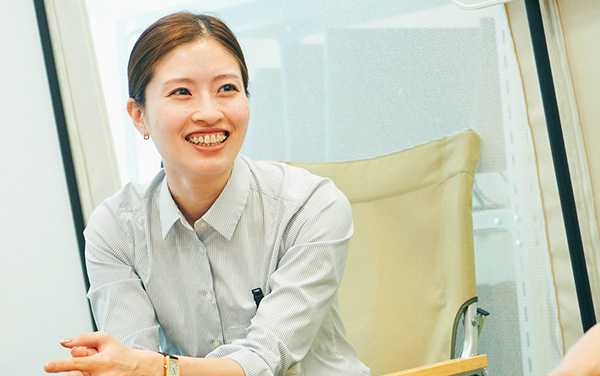
佐武「たしかに、裁量権が大きいプロジェクトでしたよね。難題続きでも仕事が楽しかったのは、裁量を持って取り組めていたからだと思います。実験結果を報告すると、知見豊富な上司たちがすぐに意見をくれて、自分になかった視点を取り入れながら進めることもできました」
伊倉「コロナウイルスの影響でちょっとした立ち話ができなくなったので、チャットツールなどで意識的にコミュニケーションを取っていました。みんなが気持ちよく仕事できるよう、私もこのプロジェクトを取りまとめる立場としてファーストリアクションの早さは心がけていました」
金「何かしらのリアクションが得られれば、次のアクションも考えやすいですしね。そしてやはり大事なのは、壁にぶつかったときに原点に立ち戻ることなのかもしれません。特別なことは必要ないのだと思います。着実にPDCAサイクルを回しながら、諦めず、粘って行動し続ける。私たちがやったことといえばそれに尽きるように思いますが、それができたからこそ得られた成果なのだと思います」

目指すは、身近な製品にCELRe®が使用されたサステナブルな未来
—今後の課題やCELRe®に期待していることを教えてください。
木下「第一に、使用するだけで環境負荷が軽減できる点は大きいので、CELRe®をより多くの方に使っていただけるよう、用途探索していくことが私たちの課題であると考えています。
現在は主に家電やオフィス家具メーカーのお客さまが中心ですが、素材としての高い強度と信頼性を武器に自動車部品への活用も進めていく予定です。一方で、お客さまにとって使い慣れた素材から新しい素材に切り替えることはコストがかかりますし、心理的なハードルもあると思います。そこをいかに取り除いていくかが重要ですね」
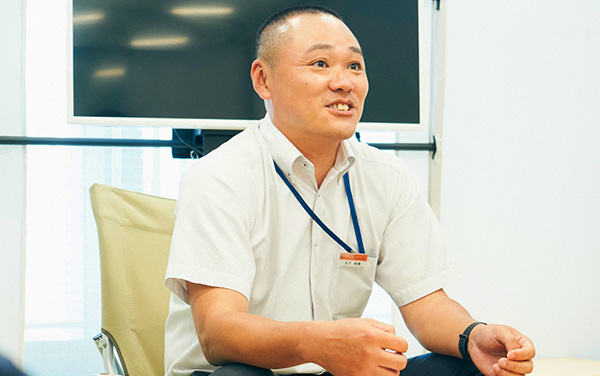
羽室「CELRe®の認知度をもっともっと高めていくことが大切ですよね。そうするとお客さま側からも『こんな製品に利用できない?』とアイデアが生まれてくるかもしれません。そのようなサイクルが生み出せれば理想ですし、一般の方が手に取る身近な製品にもCELRe®が活用されればうれしいです」
金「持続可能な社会を実現するには、一人ひとりが自分ごと化して考えることが大切だと思います。CELRe®がより身近な存在になることで、多くの人が持続可能な社会のあり方について考えるきっかけになれたらいいですね」
佐武「植物由来の樹脂の割合を現状の51%から100%にすることも進めていきたいです。それこそがCELRe®の目指すべき姿であり、これから私たちが挑戦すべきことなのだと思います」
伊倉「当社は『技術の深化と探索』を大事にしています。開発研究者はどちらかというと技術を深める“深化”に重きを置きがちなところがありますが、外の空気に触れながら視野を広く持つ“探索”も同じくらい大切です。CELRe®のプロジェクトを通してあらためてそのことを実感しましたし、今後も双方のバランスを取りながらよりよい社会をつくることに貢献したいと考えています」

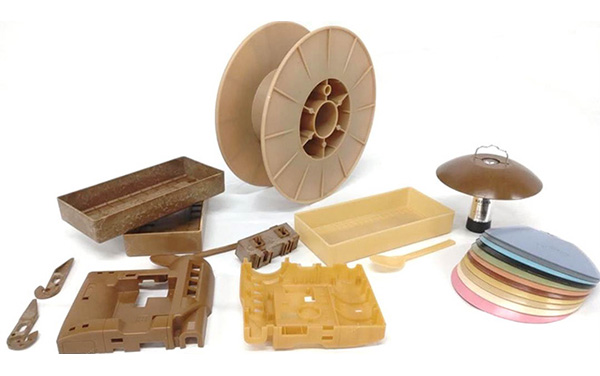