99.99%にこだわり進化し続ける無酸素銅条「GOFC®」。差別化のカギとなったお客さまの声とは
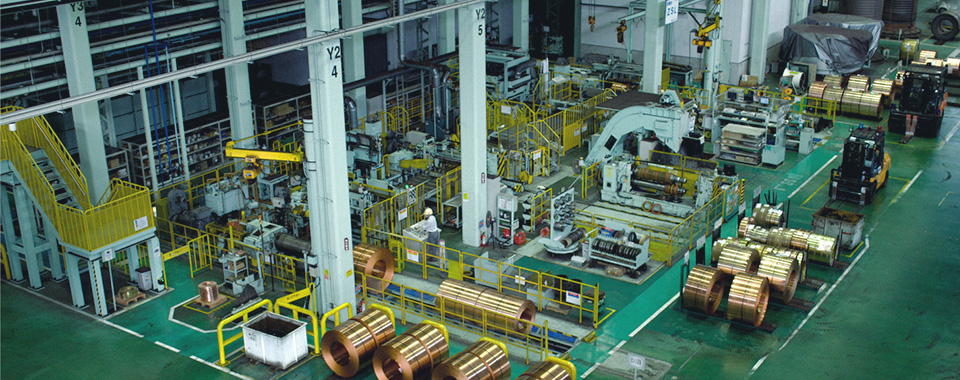
身近な存在であるものの、あまり意識されていない「銅」という金属。実は私たちが普段使用している電化製品や、電力・情報通信といったインフラには欠かせない存在です。なかでも純度が高い無酸素銅は、より高性能な電子機器や大容量通信を支える重要な役割を担っています。
古河電工が製造する無酸素銅条「GOFC®」は一般的な無酸素銅にはない「高い耐熱性」を有しており、この特長は、GOFC®を使用するパワー半導体メーカーなどお客さまが抱える課題を解決していく中で生まれました。今回は、そんなGOFC®が誕生したきっかけや改良の裏側、環境面において配慮している点などをご紹介します。
見えないところで私たちの暮らしを支える、99.99%の無酸素銅
10円玉でお馴染みの銅は、他の金属に比べて非常に電気を通しやすいことから、電子機器や電化製品などの部品に欠かせない素材として活躍しています。例えば、スマートフォンやパソコンのコネクタ、その電源アダプターから出ているコード、電信柱に張られている電線など、見えない場所で使用され、私たちの生活を支えています。
最近は次世代モビリティや、風力発電・太陽光発電などクリーンエネルギーの技術革新が進んでいることから、電力を制御する部品であるパワーモジュールの熱的・電気的負荷が急速に増大しています。それに伴い、パワーモジュールに搭載されているパワー半導体にも、より高い導電性と信頼性が求められるようになり、銅の中でも最も純度の高い「無酸素銅」が活躍しているのです。
日本産業規格(JIS)は銅の含有量が99.96%以上のものを無酸素銅(C1020)としていますが、古河電工はその規格を上回る99.99%、不純物である酸素の含有量が2ppm以下と極めて高純度な無酸素銅を製造しています。さらに、この無酸素銅をエネルギー効率の高いシャフト炉で製造することで、今後も世界的に需要の高まりが予想されるパワー半導体分野でのCO2排出量削減にも貢献しています。
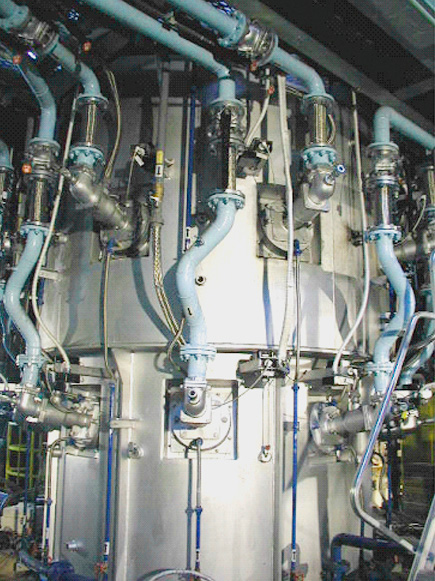
高い耐熱性をもつ無酸素銅条「GOFC®」誕生の裏側
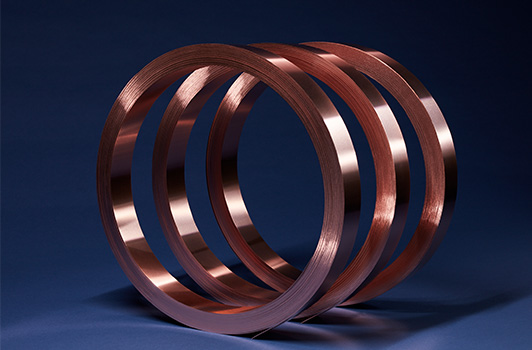
2017年、古河電工は無酸素銅(C1020)をベースに、当社の加工・熱処理のノウハウを駆使して、無酸素銅条「GOFC®」を開発しました。GOFC®の最大の特長は、なんといってもその「耐熱性の高さ」。この耐熱性を追い求めた背景には、一般的に「差別化できる要素は無い」と考えられていたJIS規格製品の無酸素銅に当社独自の強みを付加したい、そうすることでお客さまに選んでいただける製品を作りたい、という強い想いがありました。
そこで当社は、無酸素銅に対する改良ニーズを深掘りするため、約1年かけて無酸素銅を使用するあらゆるお客さまへのヒアリングを実施。集められた200件以上のVOC(Voice of Customer =お客さまの声)から、「耐熱性」が無酸素銅の課題であることに気がつきました。
パワー半導体に使用する基板は、セラミックスの板の両面に無酸素銅を高温でろう付けしているのですが、この製造工程によって無酸素銅の結晶粒が粗大化します。これは、一般的な純銅に「温度が上昇すると約500℃を境に結晶同士が結合するなどして粗大化する」という性質があるため。約800℃で高温熱処理されたパワー半導体用の基板でも、同様の変化が起こります。
そして、この「高温熱処理による結晶粒の粗大化」こそが、VOCから判明したお客様のお困りごとの原因でした。結晶粒が粗大化すると素材表面に微細な凸凹が形成され、光が当たるとキラキラと乱反射してしまうので、お客さまが光学カメラを使用して製品に傷がないかを検査する際の妨げになり、検査エラーを引き起こすという声が数多く集まったのです。
もちろん検査機器の調整で検査感度を高めることも可能ですが、当社は「キラキラしない無酸素銅」、つまり「熱が加わっても結晶粒が粗大化しない無酸素銅」を開発することで、お客さまのお困りごと解決にアプローチすることを決めました。
無酸素銅の耐熱性を向上させることは、銅の純度を高めることと相反する課題であり、開発は困難を極めました。しかし、ここでも「同じ無酸素銅でも、時々キラキラしないロットがある」というVOCが大きなヒントとなり、「キラキラしない無酸素銅」を意図的に作りこむ技術を生み出すことができました。これまで当社が独自に蓄積してきた組織制御技術を応用し、製造方法を工夫したことで、高温熱処理後も表面がキラキラしない、高純度と耐熱性を両立したGOFC®の開発に成功したのです。
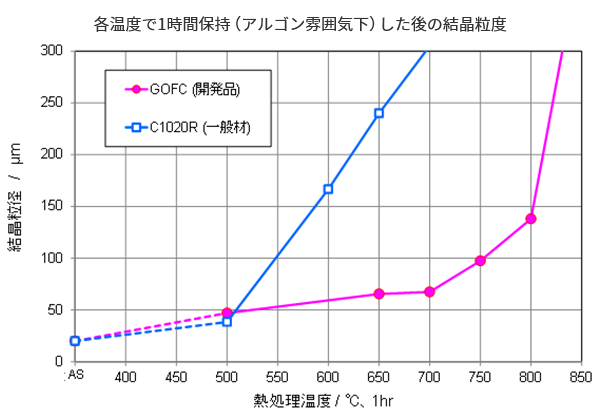
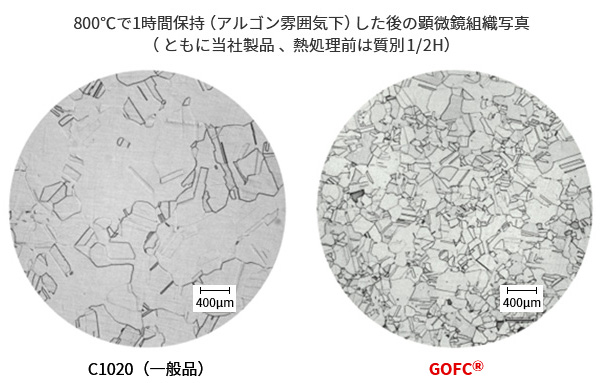
こうして開発したGOFC®をパワー半導体製品に採用していただいたところ、お客さまからは「高温処理後の検査工程でのエラーの数が減少しただけでなく、半導体チップの接合不良率も低くなった」という声が挙がってきました。当初は、GOFC®がパワーモジュールの検査信頼性アップに加え、品質安定性の確保にも貢献できるとは予想していなかったため、開発担当にとっては嬉しい結果でした。
お客さまのリアルな声に耳を傾け、開発後も改良を続ける
耐熱性という課題をクリアしたGOFC®の開発後、今度は「GOFC®の板厚のばらつきをなるべく抑えてほしい」というご要望をいただきました。お客さまが抱えていた課題は、セラミックス板に無酸素銅をろう付けする際に反りが発生し、製品の寿命が短くなるというもの。
銅板とセラミックス板は熱膨張係数が異なるため、高温で銅板を貼り付けた後、室温に戻る際の温度変化で、より収縮量の大きな銅板がセラミックス板を引っ張る力が生じます。このとき、両面に貼られた銅板の厚さに差があると、表裏面での力の差が大きくなり、基板が反ってしまうのです。
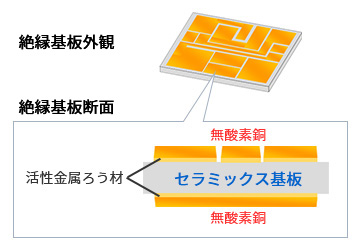
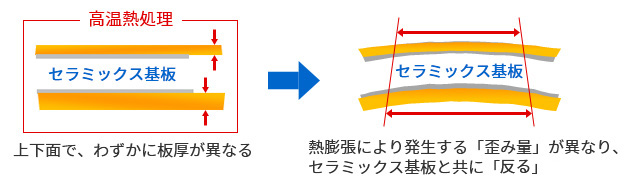
新たに生まれたこの課題に対し、古河電工は2022年、板厚を決定する仕上げ圧延工程の板厚精度を上げることで応えています。当社がもともと得意としていたリードフレーム(半導体パッケージに使用される薄板の金属)の製造で培った圧延機の板厚制御技術を活用し、GOFC®の板厚(0.25~2.0mmに対応)のばらつきを従来比1/2にまで低減させることに成功しました。
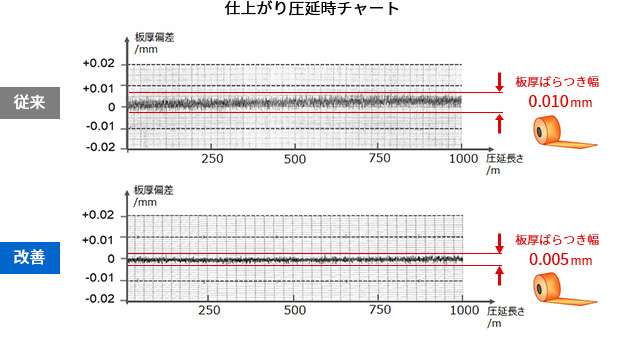
製造の川上から川下までクリーンに。バリューチェーン全体のCO2排出量削減を目指す
このように、お客さまからいただいた声をもとにGOFC®の開発・改良を重ねたことで、GOFC®を使用したパワー半導体製品の製造工程における歩留まりが高まっただけでなく、パワー半導体の寿命が延び、それを使用した製品のCO2排出量削減にも貢献できました。
さらに、当社は製造の初期段階から環境面での配慮を心がけているため、GOFC®の製造工程では当社グループの古河日光発電が100%水力で発電したクリーンエネルギーを使用しています。
銅製品に対するリサイクル要求が高まりつつある昨今の潮流に対し、古河電工ではお客さまとの間でサーキュラーエコノミー(循環型経済)構築を目指し、バリューチェーン(サプライチェーン)全体のさらなるCO2排出量削減に貢献していきます。当社は今後も環境に配慮した製品を提供し続け、お客さまとともにカーボンニュートラル社会を実現していきます。
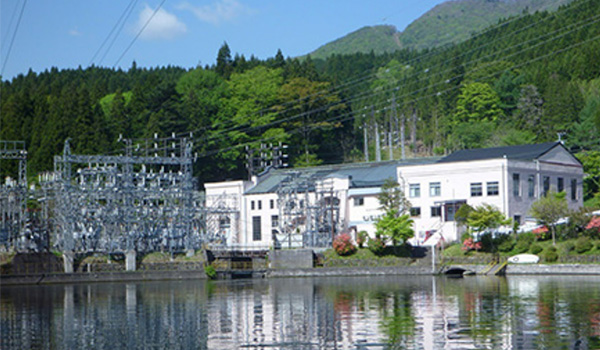