Furukawa Electric and Furukawa Develop World-leading Laser Welding Technology for Pure Copper
- Technology to significantly reduce manufacturing costs and increase performance for automobile motors and power semi-conductors -
Furukawa Electric Co., Ltd. (President: Keiichi Kobayashi, “Furukawa Electric” below) and Furukawa Co., Ltd. (President: Naohisa Miyakawa, “Furukawa” below) have jointly developed a new laser welding technology that significantly reduces welding defects in pure copper. The new technology is set to significantly reduce manufacturing costs and increase performance for automobile motors and inverter power semi-conductors, and to greatly contribute to reducing component sizes.
Background
With more vehicles being converted to EV in recent years, there are greater expectations for applying new technologies to automobile motors, inverters, batteries, and other parts. Fiber laser welding is one effective means of designing automobile parts with greater flexibility. However, pure copper easily produces welding defects such as spattering(note 1) and blowholes(note 2) due to the high thermal conduction ratio and low light absorption ratio. This has served as a major technical problem to overcome.
Content
Furukawa Electric has successfully developed a laser welding technology that significantly reduces defects that occur when welding pure copper, in cooperation with Furukawa Denshi Co., Ltd. (“Furukawa Denshi” below), a wholly-owned subsidiary of Furukawa. Through combining the “high density capacity beams” that are the strength of Furukawa Electric’s fiber lasers with “beam mode control technology” developed by Furukawa Denshi, engineers were able to form the ideal beam mode for welding pure copper—resulting in at least 95% less welding defects (spattering and blowholes) compared with conventional technologies.
This new technology is set to streamline welding and inspection processes for parts such as automobile motors and inverter power semi-conductors, contribute to significantly reducing manufacturing costs, increasing performance, and greatly reducing component sizes. Customers are able to investigate the benefits of implementing this technology at the Application Laboratory in Furukawa Electric’s Chiba Works.
(note 1)Spattering: Microparticles that scatter from fused metal when laser welding. They can cause welding defects and have a negative impact on quality.
(note 2)Blowhole: A type of laser welding defect that occurs in the weld area. It takes the shape of a round cavity within the welded metal.
Pure copper laser welding results (laser output of 6 kW, processing speed of 5 m/min)
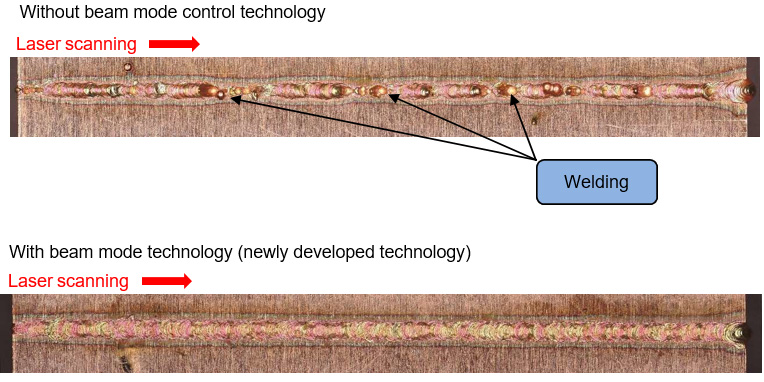
Furukawa Electric and Furukawa will continue to work together to improve welding technologies for commercial fiber lasers and to develop further solutions that leverage this technology.
About Furukawa Electric Group
Furukawa Electric (TSE; 5801, ISIN; JP3827200001) Group started business in 1884, when its copper-smelting facility and wire manufacturing factory was established. Since then Furukawa Electric has become pioneers in the latest technologies by addressing diverse technological issues. Furukawa Electric has released products in a number of areas, including telecommunications, electronics, automobiles, and construction, with the three types of materials it works with at their core, namely, optics, plastics, and metals. Many of these products have attained the top global market share, and all of its products have contributed to society in numerous business areas. Furukawa Electric reported consolidated revenues of JPY 843.3 billion (approximately USD 7.8B) for the fiscal year ended March 31, 2017.