Motors
Flat wire welding
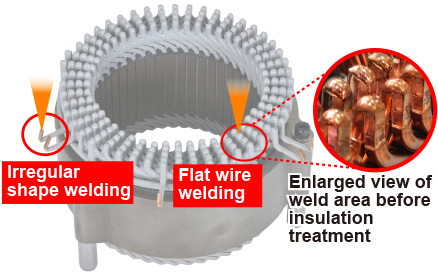
In Blue-IR hybrid laser welding, the molten pool is expanded and stabilized by the highly efficient heat input of a blue laser beam with a high absorption rate, resulting in reduced spattering and faster processing.
This is possible even if there is a gap or height difference between flat wires.
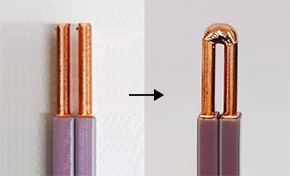
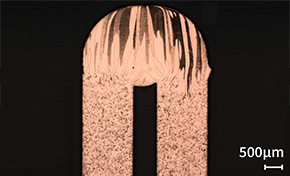
Processing conditions | |
---|---|
Output | Blue laser 1 kW + Fiber laser 3 kW |
Processing time | 100ms |
Workpiece | Oxygen-free copper flat wire |
Related product | BR1030 |
Electrolytic tough pitch (ETP) copper flat wire welding
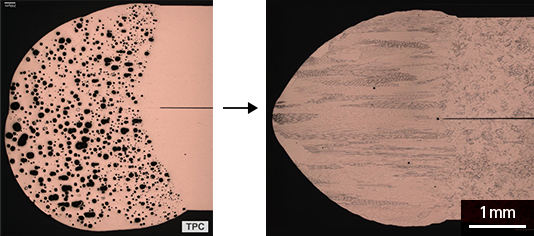
We contribute to carbon neutrality through our welding technology for ETP copper, which is often used as recycled copper but is known to be difficult to weld well due to frequent welding defects.
Processing conditions | |
---|---|
Output | Blue laser 1 kW + Fiber laser 3 kW |
Processing time | 200ms |
Workpiece | Electrolytic tough pitch copper flat wire |
Related product | BR1030 |
Insulation removal
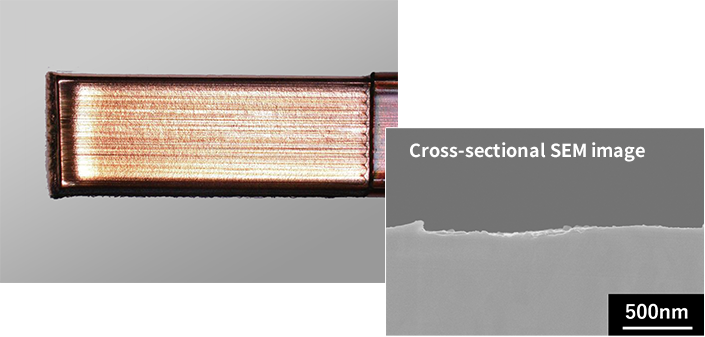
This video shows the removal of a 10 mm length. The high tolerance against focus shifting allows for the simultaneous removal of two surfaces with the wire tilted.
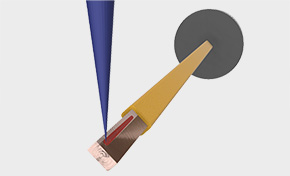
Processing conditions | |
---|---|
Output | Blue laser 400 W |
Processing time | 0.3 s for two surfaces |
Workpiece | Polyimide-coated flat wire |
Related product | BR0400 |
Inverters
Specifically designed for high-quality copper welding, Blue-IR hybrid laser technology can be used to weld various sizes and shapes, such as bus bar connections between individual components during inverter manufacturing.
Welding bus bars to substrates
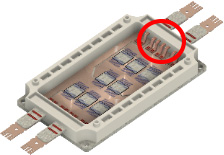
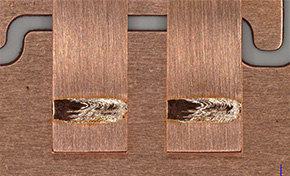
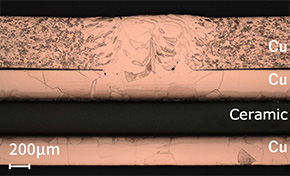
Processing conditions | |
---|---|
Output | Blue laser 1 kW + Fiber laser 1.5 kW |
Speed | 400mm/s |
Workpiece | (Upper) 0.5mmt C1020、 (Lower) Ceramic substrate, conductor layer 0.3 mm C1020 |
Related product | BR1030 |
2 mm copper lap welding
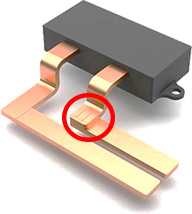
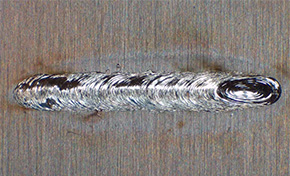
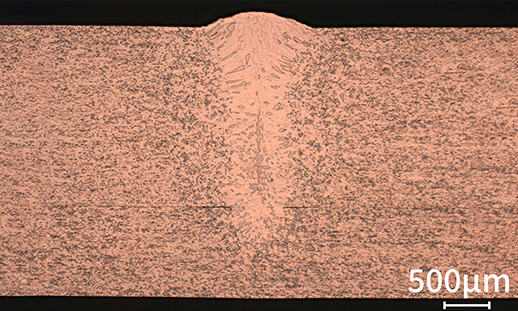
Processing conditions | |
---|---|
Output | Blue laser 1.5 kW + Fiber laser 4.5 kW |
Speed | 150mm/s |
Workpiece | (Upper) 2mmt C1020、(Lower) 1mmt C1020 |
Related product | BR1030、BR1545、BR2200+FEC6000M |
5 mm copper butt welding
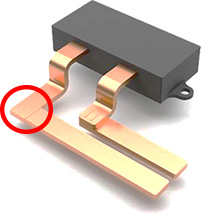
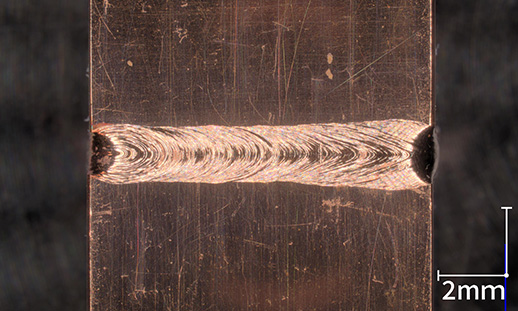
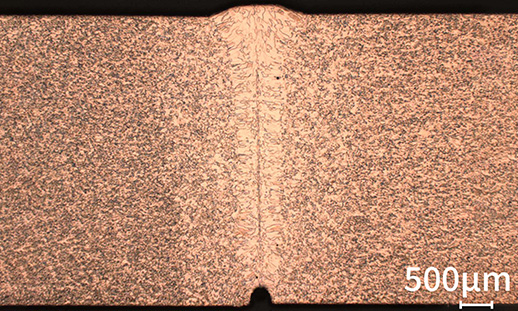
Processing conditions | |
---|---|
Output | Blue laser 1.5 kW + Fiber laser 4.5 kW |
Speed | 100mm/s |
Workpiece | (Upper) 2mmt C1020、(Lower) 1mmt C1020 |
Related product | BR1030、BR1545、BR2200+FEC6000M |
Inquiries about Industrial Lasers