- Flexible beam forming technique using an optical head equipped with beam mode control function
- Spatter reduction with beam mode control
- Mechanism for eliminating spatter and blowholes with beam mode control technology
- Comparison of welding quality
- Beam mode control technology application examples
Flexible beam forming technique using an optical head equipped with beam mode control function
(Note) The optical head with beam mode control function was jointly developed with Furukawa Denshi Co., Ltd.
The key feature of our beam mode control technology is flexible mode design. The beam mode can be changed to the desired shape to obtain the optimum pattern and intensity distribution for each workpiece.
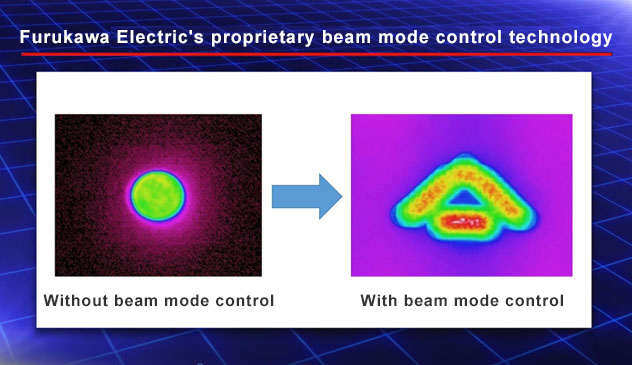
Beam forming principle and beam mode design
-
Principle of light diffraction
Diffraction occurs when plane waves pass through the slits. This causes wave crests to intensify as they overlap, and the white area becomes diverged light.
-
DOE image
Diffractive optical elements (DOEs) use this principle to split the laser beam.
Design specifications
- The light profile is simulated from the design parameters (wavelength, optical system magnification, desired beam mode shape).
- By forming a multilevel structure with information on different grating periods, it is possible to obtain a multi-branch beam mode pattern of controlled branched light intensity.
- The DOE obtained with Furukawa Electric's proprietary technology is characterized by high efficiency and high positional accuracy.
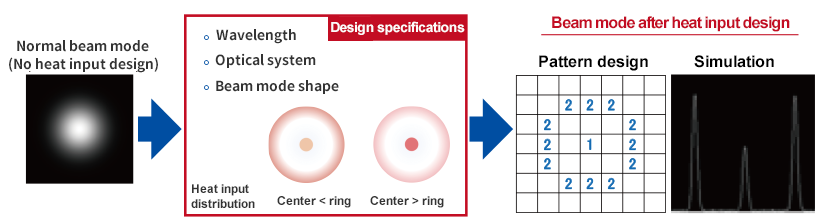
Spatter reduction with beam mode control
Spattering can be dramatically reduced by applying beam mode control technology.
The processing quality improvement effect obtained with beam mode control technology can be verified at our Chiba Works' Application Lab, or at our external partner laboratory in the Chubu District.
Beam mode control technology offers dramatic benefits for the welding of various materials (highly reflective materials such as zinc-plated steel plate, high-strength steel sheet, aluminum alloy, iron, stainless steel, copper, aluminum) that require the suppression of spattering and blowholes.
Without beam mode control (Normal light condensing) |
With beam mode control | |
---|---|---|
Aluminum alloy | ![]() |
![]() |
Stainless steel (SUS304) |
![]() |
![]() |
The mechanism for eliminating spatters and blowholes using beam mode control technology
Spatter and blowholes can be reduced by heat input design that matches the customer's material, process, and cycle time.
-
Conventional technology
Issues in high-speed (high power) processing
- Local heat input distribution in the keyhole
Fluidity turbulence due to induced vapor
Spatters and blowholes generated
Spatter : Scattering of molten metal
Blowhole : A bubble hole that remains in welded metal - Local heat input distribution in the keyhole
-
Beam mode control technology
High-speed processing with DOE, matches customer's material, process and cycle-time.
- Preheating effect around keyhole
Vapor pressure is dispersed to the surrounding area and fluidity is rectified
Achieves high quality weld by achieving spatterless and blowholeless
- Preheating effect around keyhole
Comparison of welding quality
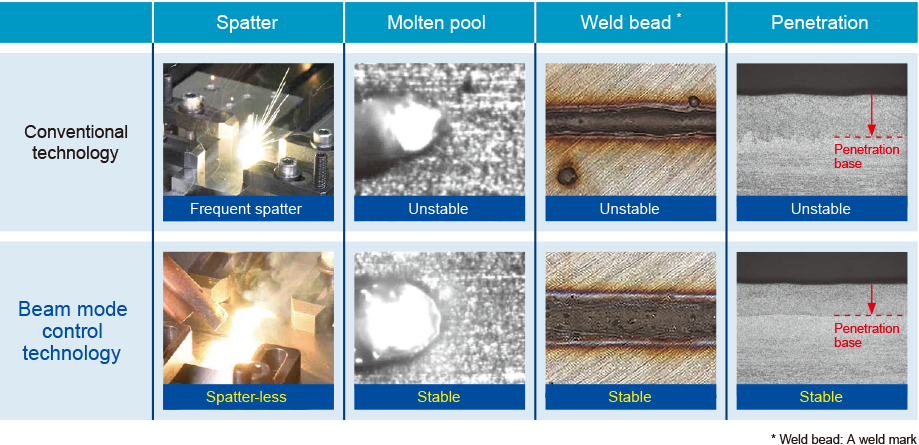
Beam mode control technology application examples
Field | Processing types | Details | Application field | |
---|---|---|---|---|
Laser processing | Welding |
|
Various types of welding requiring suppression of spattering and blowholes
|
|
Reforming |
|
Heat treatment in wider range with controlled heat input to workpiece surface layer
|
|
|
Removal |
|
More extensive cleaning of work surface layers
|
|
Inquiries about Industrial Lasers