Furukawa Automotive Systems to Being Selling Automatic Cutting and Crimping Equipment to Spread “α Terminal Series” Worldwide
- New product set to accelerate conversion to aluminum harnesses and help to make greener cars -
Furukawa Automotive Systems Inc. (Headquarters: Inukami-gun, Shiga Prefecture; President: Katsumi Shibata; “Furukawa Automotive Systems” below), a member of the Furukawa Electric Group, has developed and will begin selling new automatic cutting and crimping equipment compatible with anti-corrosion terminals (“α Terminal Series” below) used for aluminum wires in vehicle wire harnesses (“W/H” below).
In addition to expanding the use of α Terminal Series from four-wheeled vehicle to two-wheeled vehicles, Furukawa Automotive Systems will use this opportunity to begin selling α Terminal Series (which previously had been used only on Furukawa Automotive Systems W/H) to other companies in the W/H industry and connector manufacturers inside and outside Japan, to help spread the use of α Terminal Series throughout the world.
Background
The conversion of copper wire W/H to aluminum has been gaining attention due to the need to lighten vehicles and the rising cost of copper resources.
Furukawa Automotive Systems was the first in the world to successfully develop “α Terminal Series” anti-corrosion terminals for aluminum wire W/H, which can be used with existing connector housings and that offer world-class anti-corrosion performance and lower anti-corrosion processing costs. Furukawa Automotive Systems plans to continue expanding its product lineup—for example, a total of 21 types of products are produced at its Mie Works location.
Content
Furukawa Automotive Systems has jointly developed automatic cutting and crimping equipment for “α Terminal Series” together with a general cutting/crimping equipment manufacturer, and will begin selling the equipment in April of this year.
The new automatic cutting and crimping equipment was developed based on manufacturing systems that have been successfully used in Furukawa Automotive Systems W/H manufacturing sites. It incorporates operations to insert wires into tubular terminals (a core technology required for terminal crimping) and multilevel crimping operations performed with a digital crimper(note 1), and is equipped with sensors used to detect crimping loads and wire insertion amount—resulting in high quality cutting and crimping.
In addition to double-ended α terminals, the new equipment can also be used for high-speed double-ended simultaneous crimping of conventional open barrel terminalss(note 2) by switching the applicator.
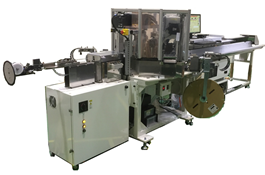

(note 1)Multilevel crimping operations performed with a digital crimper: Multi-position stop operations driven by servo motors during the crimping process.
(note 2)Open barrel terminal: The main terminal used in the W/H industry, where the upper surface of the swaged portion of the terminal’s core is open.
Furukawa Automotive Systems will work toward accelerating the conversion of copper wire W/H to aluminum wire W/H, and help to create greener cars by selling this new automatic cutting and crimping equipment in locations such as Asia, Europe, and the US, and by promoting the spread of “α Terminal Series” throughout the world.
About Furukawa Electric Group
Furukawa Electric (TSE; 5801, ISIN; JP3827200001) Group started business in 1884, when its copper-smelting facility and wire manufacturing factory was established. Since then Furukawa Electric has become pioneers in the latest technologies by addressing diverse technological issues. Furukawa Electric has released products in a number of areas, including telecommunications, electronics, automobiles, and construction, with the three types of materials it works with at their core, namely, optics, plastics, and metals. Many of these products have attained the top global market share, and all of its products have contributed to society in numerous business areas. Furukawa Electric reported consolidated revenues of JPY 843.3 billion (approximately USD 7.8B) for the fiscal year ended March 31, 2017.