New Laser Welding Machine for Motors of Electric Vehicles (EV) Developed
- Provides a one-stop solution for everything from winding to assembly and welding to testing -
- Through the co-operation of the precision FA technology of NITTOKU and the laser processing / copper material characterization technology of Furukawa Electric, we can provide one-stop service including labor saving FA systems, high-quality laser welding technology, and after-sales service.
- Achieves 10 times faster cycle time and overwhelmingly high-quality welding with the new laser welding machine, enabling improved production efficiency.
- Both companies will contribute to a sustainable society through the realization of highly efficient drive motors for EV.
NITTOKU Co., Ltd. (Headquarters: 2-292-1, Azumacho, Omiya-ku, Saitama City, Saitama; President: Nobushige Kondo; “NITTOKU” below) and Furukawa Electric Co., Ltd. (Headquarters: 2-3, Marunouchi 2-chome, Chiyoda-ku, Tokyo; President: Keiichi Kobayashi; “Furukawa Electric” below) have jointly developed a laser welding machine for EV motors. Together, they hope to bring efficiency to their customers’ motor manufacturing processes (accelerating work, simplifying processes, and stabilizing quality), by combining the factory automation (FA) solutions of NITTOKU (which boasts the top market share in the world for winding machines) and the laser welding copper material characterization technologies of Furukawa Electric.
The new product will be revealed for the first time during Photonix2020, which is scheduled to be held from December 2nd to December 4th. A demonstration will be performed showing hairpin welding of a rectangular magnet wire. The exhibited machine will feature the new Furukawa Electric Blue-IR hybrid laser and scanning system, allowing it to measure rectangular magnet wire arrangement errors, and to weld with the laser scanning in the optimal position.
Background
EV technologies are expected to account for an increasingly larger proportion of the automotive market. As the main driving force of these vehicles, motors will need to become smaller, lighter, and more efficient.
Motors that use rectangular magnet wire are becomingly increasingly commonplace in situations requiring smaller high-power motors. TIG welding(note 1) is generally used to weld these rectangular magnet wires. However, this method cannot be used to selectively melt a given area, so rectangular wires must be arranged with a high level of accuracy. Lasers, however, provide non-contact processing and are therefore well-suited for image processing technology and are capable of selectively melting a given area. They also have little heat input and can be used for efficient welding.
However, pure copper has high thermal conductivity and low light absorption rate at the wavelength of a fiber laser. This makes it difficult to control heat input and to reliably form weld pool and keyhole shapes. It can also result in processing defects such as spattering and blowholes.
Details
Overview of system/technology
- The new product is a laser welding machine for motors of EV. During the welding process, both quality and production can be increased due to the combination of the precision FA technologies of NITTOKU and the laser processing technologies of Furukawa Electric (beam mode control(note 2) and Blue-IR hybrid laser technologies(note 3)).
- In addition to precision processing using rectangular wire forming, NITTOKU will install a production facility line that makes use of original control technology to further improve the performance of Furukawa Electric laser oscillators.
- Furukawa Electric laser processing technologies are used to allow motor welding to be performed even when there is a difference in height or gaps between rectangular wires, allowing the process to be simplified.
- NITTOKU will start accepting orders for this new product in December 2020. Interested customers will be provided with machine specification proposals based on the shapes and sizes of their motors, as well as the processes they use.
- Customers with plants outside of Japan will be provided with maintenance and support from their nearest NITTOKU site.
Glossary
(note 1)TIG welding: A type of arc welding that uses electricity. A high voltage is applied between the electrode and base metal. As the high current flows, the heat generated by the arc discharge is used to produce the weld. It is suited for welding all sorts of metals such as iron, aluminum, and copper.
(note 2)beam mode control: Technology that controls the beam shape of a laser using a beam mode conversion element. By stabilizing the molten pool of the laser irradiation part, it is possible to realize high quality laser welding such as prevention of spatter and internal defects.
(note 3)Blue-IR hybrid laser technologies: A combination of a blue laser (wavelength: 465 nm) that has high light absorption rate for copper and a near-infrared laser (wavelength: 1070 nm) that provides deep penetration. The light absorption characteristics of the blue laser enable stable heat input control, enabling copper welding that achieves both high speed and high quality.
Furukawa Electric Group’s efforts towards the SDGs
Based on the corporate philosophy of “Drawing on more than a century of expertise in the development and fabrication of advanced materials to contribute to the realization of a sustainable society through continuous technological innovation,” the Furukawa Electric Group is conducting business activities centered on four core technological capabilities (metals, polymers, photonics and high frequency). Moreover, keeping in mind the “Sustainable Development Goals (SDGs)” adopted by the UN, we formulated the “Furukawa Electric Group Vision 2030,” which clarified the business areas of the Furukawa Electric Group, and are advancing efforts aimed at “creating solutions for the new generation of global infrastructure combining information, energy, and mobility to build a sustainable world and make people’s life safe, peaceful, and rewarding.
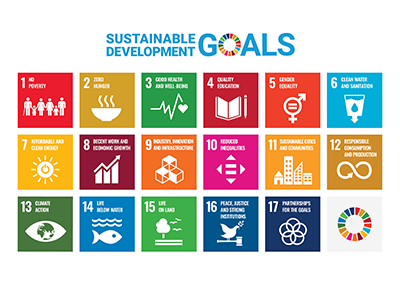
Inquiries about the product
NITTOKU Co., LTD.
Sales support section
Global sales division
Akihiko Kayano
E-MAIL:a-kayano@nittoku.co.jp