Furukawa Automotive Systems begins delivering High-Voltage Power Distribution Component Modules for Toyota MIRAI (Hydrogen Fuel Cell Vehicle)
- Development of new components supporting the electrification of automobiles contributes to reducing CO2 -
- Furukawa Automotive Systems has begun supplying high-voltage power distribution component modules for use in the FC systems of new Toyota MIRAI model vehicles.
- The highly accurate and compact modules help to make FC system assembly work easier.
- Furukawa Automotive Systems contributes toward promoting the adoption of electric vehicles and achieving carbon neutrality by 2050 through development of automotive components.
Furukawa Automotive Systems Inc. (Headquarters: Inukami-gun, Shiga Prefecture; President: Shigenobu Abe), a member of the Furukawa Electric Group, has delivered modules for use in the fuel cell (FC) systems of new Toyota MIRAI model vehicles. Based on technologies developed by Furukawa Automotive Systems in the auto power distribution components business, these high-voltage power distribution component modules(note 1) are highly efficient and compact.
Background
Global warming caused by increased emission of carbon dioxide and other greenhouse gases has caused various climatic anomalies and has become a major ecological issue throughout the world. In response, the Japanese government announced its intention to become carbon neutral by 2050 and has formulated its “Green Growth Strategy Through Achieving Carbon Neutrality.” Among other objectives, the strategy calls on the automotive industry to ensure that all new vehicles sold are electric vehicles by the mid 2030s. This is forecast to accelerate the adoption and use of electric vehicles and hydrogen fuel cell vehicles. Hydrogen fuel cell vehicles in particular have attracted attention as the ultimate ecologically friendly car, as these vehicles use hydrogen as fuel and are capable of completely eliminating the emission of harmful gas.
Details
The high-voltage power distribution component modules that were recently delivered connect components electrically in the FC stack(note 2) and boost converter, allowing for high-voltage and high-current power to be distributed. An FC stack is a type of power generator used in fuel cell vehicles. The power it generates is boosted up to a maximum of 650 V by an FC boost converter and then distributed to devices such as the PCU.
Feature 1: Bus bar module method results in high-accuracy and high-density high power transmission
Although FC system components are connected together electrically in multiple locations, they are generally bolted or welded together and use bus bars(note 3) as the transmission media. Components installed in the system must be connected together in multiple locations, and a high degree of positional accuracy is required when assembling these components to each bus bar. There is also only limited space for bus bar routing(note 4). Routing must therefore be efficient while also ensuring sufficient insulation from other components. In order to ensure workability during the assembly process, it is also important that products remain free-standing after they are temporarily retained in place and that the bus bar position does not shift. Furukawa Automotive Systems has leveraged the operations management engineering technologies it has developed over many years to optimize its manufacturing management and inspection processes during the stamping, insert molding(note 5), and assembly processes, resulting in superior positioning accuracy.
In order to meet this requirement, this product makes use of the bus bar module method in which bus bars are insert molded. Standard copper is used for the conductors, and the product was designed with recyclability in mind. Engineering plastic was chosen as the resin material in order to withstand high-temperature environments, due to its high heat resistance and low thermal stress near the linear coefficient of expansion for copper. Materials were carefully selected and the structural design was optimized, resulting in a highly efficient routing structure and excellent workability during assembly.
Feature 2: 23% more compact than the previous model
Although the FC system of the new model has a higher maximum output and loaded current compared with the previous model, the module structure allows bus bars to be routed at minimum pitch, resulting in an approximately 23% reduction in overall size—even considering the increase in size due to the higher loaded current. This has helped result in an FC system with an output density (output per unit capacity) that is among the best in the world.
When using insert molding, differences in the linear coefficient of expansion for each component can cause issues with thermal stress due to the heat generated from nearby components and the increase in internal temperature during current loading. In order to prevent resin from cracking due to thermal stress, a thermal stress analysis simulator was used to predict internal stress prior to setting the optimal bus bar layout and resin thickness at each location. A resin flow analysis was also conducted in order to take resin orientation and welding areas into consideration during molding, in an attempt to reduce thermal stress.
The Furukawa Electric Group will continue to develop products in order to help promote the adoption and use of electric vehicles and contribute toward achieving carbon neutrality by 2050.
Product photo (size comparison with 500 yen coin)
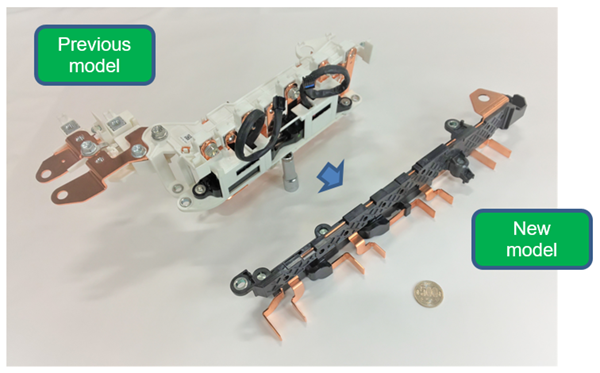
Terminal block (module) layout diagram
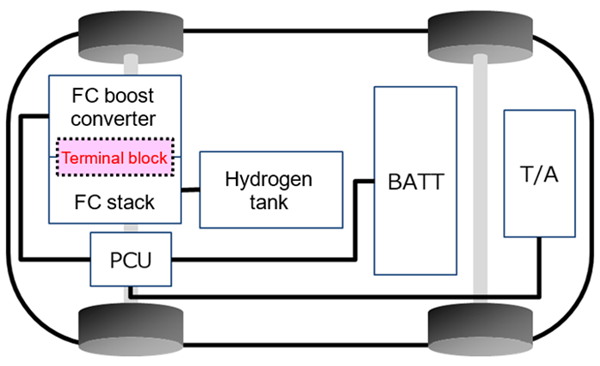
Glossary
(note 1)Module: A component with cohesive functionality that integrates multiple components. This product integrates the bus bar that serves as the transmission medium for power, resin components that ensure sufficient insulation performance, and anchoring components (nuts, collars) for other components.
(note 2)Fuel cell (FC) stack: A type of power generator installed in a fuel cell vehicle. A fuel cell generates power through creating a chemical reaction in hydrogen and oxygen. The simplest structural unit of a battery is called a cell. A single cell is capable of generating only a small amount of power, so several hundreds of cells are layered in series in order to obtain the required voltage in actual use. Fuel cells layered in this manner are referred to as an FC stack.
(note 3)Bus bar: A conductor component used to transmit high current. Copper is mainly used as the material. Stamping is used to punch-out or bend strip material into the required shape.
(note 4)Routing: A process by which the routes of bus bars connecting components electrically are designed and arranged to fit within a limited space.
(note 5)Insert molding: A type of molding. A component is inserted into a mold for injection molding and then melted resin is injected around the component. This results in the inserted component becoming integrated with the resin component. Insert molding is used to integrate bus bars, nuts, collars, and resin components in this product.
Furukawa Electric Group’s efforts towards the SDGs
Based on the corporate philosophy of “Drawing on more than a century of expertise in the development and fabrication of advanced materials to contribute to the realization of a sustainable society through continuous technological innovation,” the Furukawa Electric Group is conducting business activities centered on four core technological capabilities (metals, polymers, photonics and high frequency). Moreover, keeping in mind the “Sustainable Development Goals (SDGs)” adopted by the UN, we formulated the “Furukawa Electric Group Vision 2030,” which clarified the business areas of the Furukawa Electric Group, and are advancing efforts aimed at “creating solutions for the new generation of global infrastructure combining information, energy, and mobility to build a sustainable world and make people’s life safe, peaceful, and rewarding.
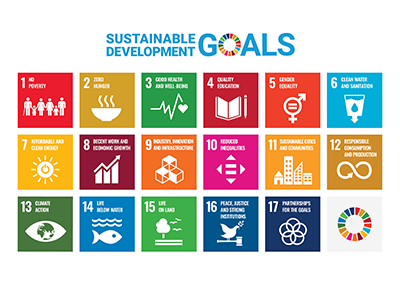