Electronics Component MaterialsLeveraging the development capabilities for high performance materials and contributing to the advancement of electronics technology
Made up of the electric conductor (including magnet wire) business and the copper & high performance material products business, the segment manufactures and sells mainly copper products for electrical wire, automotive components and electronics materials.
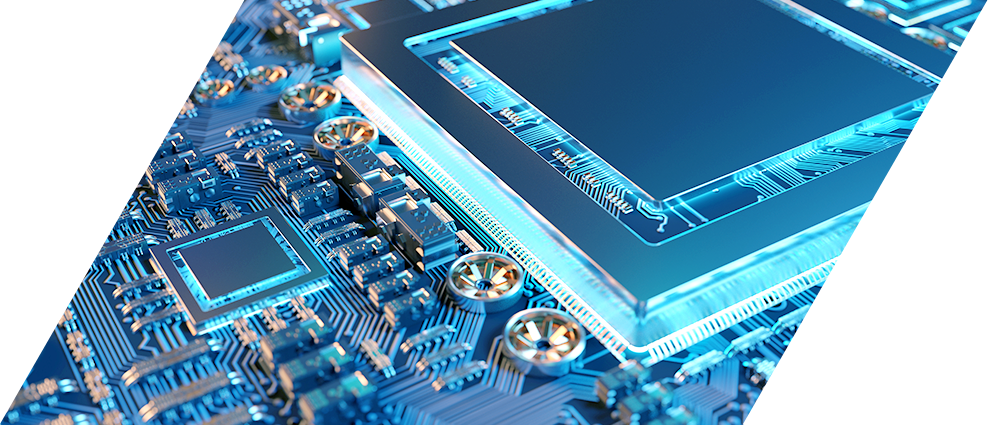
Business environment and background
Growing demand for high performance devices that support vehicle Electrification and Autonomous driving
In recent years, vehicle digitalization has progressed along with the progress of ADAS (Advanced Driver-Assistance Systems) in advanced vehicles and autonomous driving technology. Following this, individual components are also required to have high precision and high reliability, and the demand for higher performance communications devices, sensors, control devices and passive components is growing.
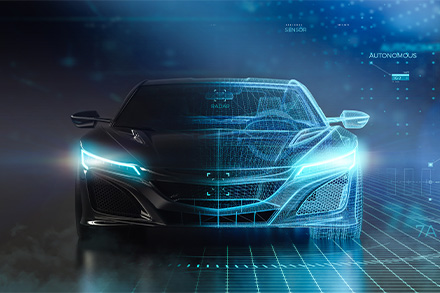
Increased demand for high performance products following the growth in data traffic
Data traffic is growing following the rapid introduction of DX and AI with an eye toward Beyond 5G. In the telecommunications and electronics markets, there are increasing needs for non-magnetic products to prevent malfunctions and products with good thermal dissipation properties to limit heat build-up in devices. Needs are also increasing for high performance connector materials used to connect the thermal dissipation products. In the semiconductor and electronic component markets that are expected to grow further in the future, there will likely be increasing demands for higher performance materials.
Based on these needs, our Electronics & Automotive Systems business is working to develop, manufacture and sell electrical wire with added value that satisfies various requirements, as well as materials used in advanced automobiles and advanced electronic devices.
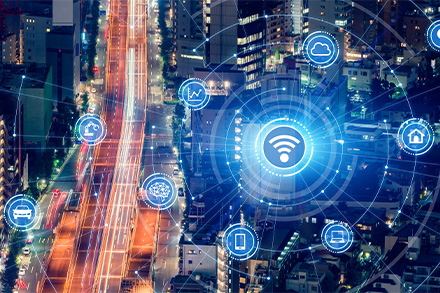
Business domains and strengths
Ability to respond to new needs and trust in the technology backed by the group’s history and achievements
Furukawa Electric’s high purity oxygen-free copper features world-class purity of ≧99.99%. It has high electrical and thermal conductivity, and it is used in a wide range of electronic devices and in-vehicle components. It is also used as the shielding material for submarine optical cable, and with a global share of about 33%, our oxygen-free copper contributes to the stability of the global telecommunications network.
In this way, the trust in our technology backed by years of experience and the ability to propose and develop materials that respond to new needs are several of our strengths.
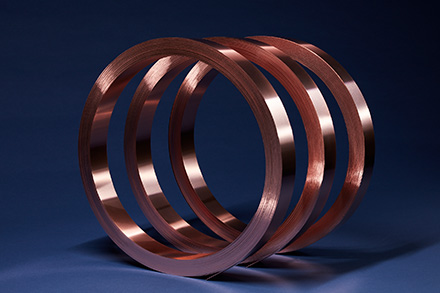
Realizing a clean production system from the upstream through the downstream manufacturing processes
Our group company Furukawa Nikko Power Generation operates a hydroelectric power station that uses a natural lake as the power source. The Nikko Works uses this clean hydroelectric power for 100% of the electricity used. Therefore, our CO₂ emissions are greatly lower than our competitors, and we supply the market with copper and copper alloy products manufactured through a low carbon process.
In addition to supplying such products (Scope 2 emissions in the supply chain), we also contribute to reducing CO₂ emissions throughout the value chain (Scope 3 emissions in the supply chain) by actively promoting recycling.
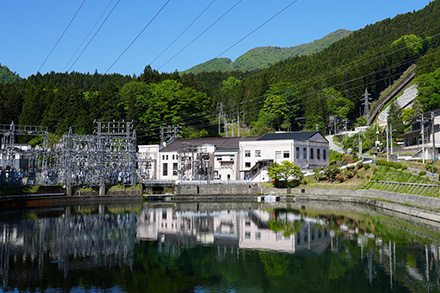
Medium-term business strategy (2025)
Accelerate vehicle electrification through oxygen-free copper strips
Following the introduction of Evs including electric cars, the adoption of drive motors has progressed, and the demand for power modules is growing. Also, given the increased needs for power semiconductor devices, which transform and control the electric power, the demand for oxygen-free copper with excellent thermal conductivity is increasing for the connections between components. In addition, demand is also increasing for the resistance material used to display the remaining charge in smartphones and vehicle BSS (lead-acid battery state sensor).
Given this, we have further improved our high purity oxygen-free copper with the impurities such as oxygen removed using our own proprietary technology to realize “GOFC” oxygen-free copper strips with increased heat resistance.
Above: Junction box equipped with a power semiconductor
Below: Example of an installed BSS
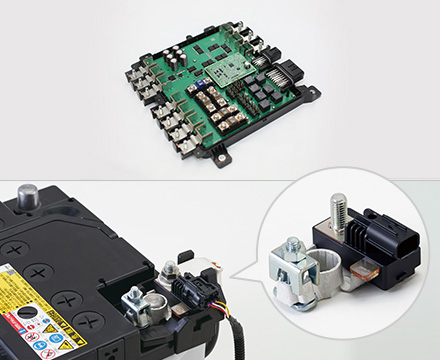
In the power semiconductor chip equipped in power modules, oxygen-free copper is bonded to an insulating substrate, but when general-use oxygen-free copper is used, it tends to become discolored by the heat treatment in the manufacturing process. In comparison, GOFC with its high heat resistance successfully reduces this discoloration. It also leads to reduced deformation of the insulating substrate and increased product reliability and longevity.
Demand for oxygen-free copper is expected to further grow in the future. Given this, directed at FY2025, we will prepare a framework for increasing production, and while aiming to increase sales five-fold (compared to FY2021), we will greatly contribute to vehicle electrification.
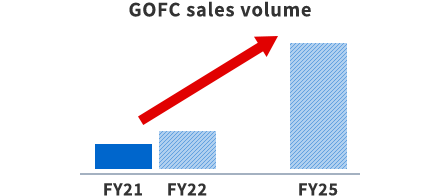
Increase enameled wire production capacity, and contribute to the growing electronic products market
Enameled wire has excellent insulation and heat resistance, and it is used for coils in inductors and other components in electronic devices and telecommunications devices.
Furukawa Electric Group’s enameled wire includes a broad lineup of products for various applications, including an easily processed type, highly smooth type and rectangular type. All types make it possible to reduce coil size, increase the coil space factor and increase efficiency, and they also contribute to streamlining work operations and reducing the nonconformance ratio. In addition, the high durability of the enameled wire, which can withstand years of use, will lead to long-term quality assurance.
Enameled wire is essential for advanced telecommunications technology, including the micro-speakers and condensers in smartphones, as well as for Evs and autonomous driving, and demand is expected to grow in the future. Going forward, we will increase enameled wire production capacity and contribute to the electronic component market.
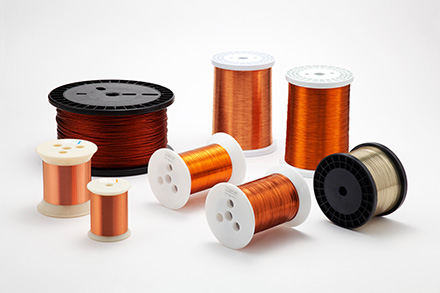
Supporting advanced medicine, which requires high reliability, through Ni-Ti (nickel titanium) alloy
This unique alloy made from nickel and titanium (Ni-Ti alloy) is flexible enough to withstand major deformation without breaking, and it also returns to its original shape.
Furukawa Electric Group’s Ni-Ti alloy is making great contributions to the medical domain. In recent years, following the increased needs for minimally invasive procedures, which decrease the burden on the patient’s body, demand has rapidly increased for medical devices that require smaller incisions and reduce recovery time. Within this trend, Furukawa Electric’s Ni-Ti alloy is used as a material for medical devices, such as the guidewires and stents used in catheter procedures for the circulatory system, including heart attacks and strokes.
Going forward, in response to the expected demand growth for advanced medical products, we will focus on further increasing Ni-Ti alloy production capacity and developing new products.
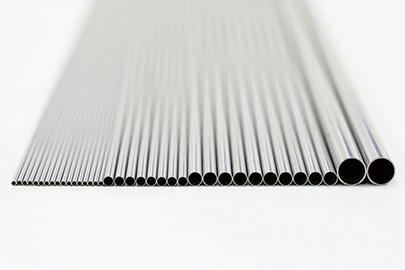
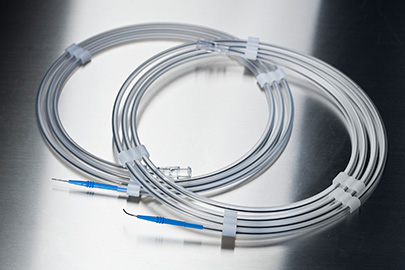
Products
Product website
Furukawa Electric Group, Vision 2030
Special site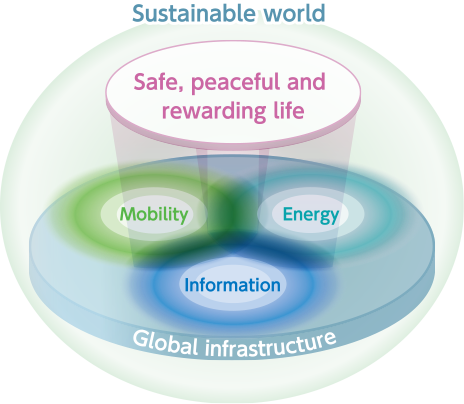