Launching Sales of the “BRACE™” Blue-IR Hybrid Laser
- Achieving the world's highest level of copper welding quality, depth, and welding speed for key xEV parts -
- Launching sales of “BRACE™”, a Blue-IR hybrid laser that combines a blue direct diode laser(blue-DDL) with a high-brightness blue laser diode module (LDM) and a near-infrared (IR) fiber laser
- Contributing to greater productivity for key electric vehicle (xEV) parts and manpower savings for manufacturing processes
- Future plans include further increasing the power of blue LDMs and developing next-generation hybrid laser through joint development with Nichia Corporation.
On January 18, 2021, Furukawa Electric Co., Ltd. (Head Office: 2-2-3, Marunouchi, Chiyoda-ku, Tokyo, President: Keiichi Kobayashi) will launch sales of “BRACE™” (trademark registration pending), a Blue-IR hybrid laser that combines a blue-DDL and a near-infrared (IR) fiber laser.
This laser is equipped with the high-brightness blue LDM that was jointly developed with Nichia Corporation (Head Office: 491 Oka, Kaminaka-Cho, Anan-Shi, Tokushima, President: Hiroyoshi Ogawa) that announced on June 5, 2020. Based on energy conversion efficiency of blue-LDM’s, this laser will significantly contribute to greater productivity in copper welding processes. In the future, we will further increase the power of the blue LDM and develop and commercialize next-generation hybrid lasers in order to improve the productivity of copper welding in a wide range of applications, including key xEV parts, and manpower savings in manufacturing processes.
On January 25, 2021, we will open the “Application Lab” equipped with this laser at the Furukawa Electric Chiba Works to enable test of samples by customers.
Background
Countries around the world have recently been developing xEVs that emit no NOx, PM, or CO2 when in operation in order to protect the global environment. From the viewpoint of preventing transmission of the novel coronavirus virus (COVID-19), which continues to spread throughout the world, various countries have also been developing approaches replacing humans with robots and unmanned transportation technologies. Likewise, the availability of xEVs, which have a high affinity with these technologies, is expected to accelerate. Given these circumstances, production volumes for batteries, motors, inverters, and other parts that are essential for xEVs are anticipated to increase dramatically. This will in turn drive the desire for greater productivity (higher quality and welding speeds) in copper conductor welding processes and for manpower savings in manufacturing processes.
At the same time, investigations have been made into replacing ultrasonic welding and arc welding with laser welding in order to increase welding speeds. Fiber laser has high-brightness, high speed, and a high welding depth, but it has also has technical issues; these have difficulty achieving a stable heat input, making for problems with welding defects (spattering, blowholes) result in a low light absorption rate with copper. Meanwhile, short-wavelength lasers have a high light absorption rate and thus enable stable heat input with copper, but the large beam diameter makes it difficult to achieve high-speed, high-depth welding.
In contrast, this hybrid laser consists of a short-wavelength blue-DDL and a near-infrared (IR) fiber laser, and thus achieves the world's highest level of quality, depth, andspeed during copper welding by applying the strengths of each to compensate for their respective weaknesses. (Figure.3)
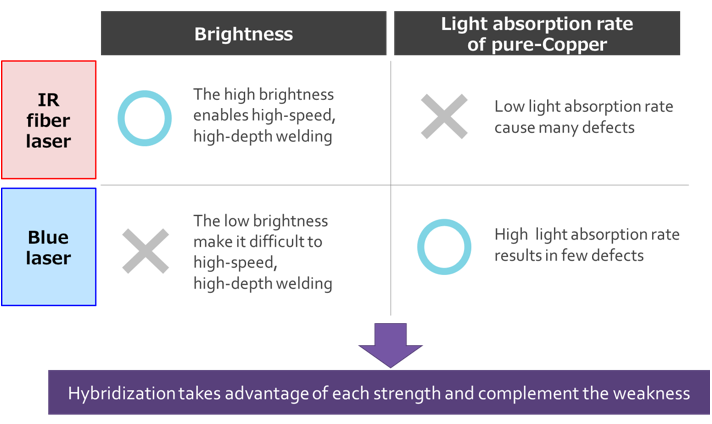
Details
Equipment specifications
- This hybrid laser combines a 150 W blue-DDL (110 μm core diameter) and a 1 kW near-infrared (IR) fiber laser (14 μm core diameter), with the world's highest level of power density.
- Each power and timing of the blue-DDL and fiber laser can be centrally controlled.
Welding example
This welding example assume the use of this laser to weld pure copper in the lithium ion battery manufacturing process. This laser achieves high-quality welding with few welding defects on the surface and inside.
● Welding of 8 μm thick copper foil (50 sheets) on a 0.5 mm thick current collector (copper plate)
Product roadmap
- In order to continue providing customers with high-speed, high-efficiency laser welding processes while maintaining welding quality, we will pursue the development and commercialization of high-performance laser oscillators together with Nichia Corporation as our partner in joint development.
- Specifically, in order to expand the range of xEV part applications, we plan to develop lasers suited to thick and large-diameter samples by continuing to increase the output of blue LDMs.
- We will continue to develop applications for key xEV parts (including lithium ion batteries, motors, and inverters) and develop laser oscillators that contribute to higher performance xEVs.
Application Lab (prototype welding laboratory)
- On January 25, 2021, we plan to open application laboratory at the Furukawa Electric Chiba Works to provide hands-on experience with the effectiveness of this laser.
- Along with Furukawa Electric’s accumulated laser welding technologies (“Beam Mode Control Technology” for improving welding quality and “Ultrafast Optical Pulse Waveform Control Technology” specialized in cutting metal battery foils), we can propose a wide range of welding solutions tailored to specific applications (materials, shapes).
- We will put together an online test environment utilizing a web conferencing system to enable remote observation and prototype handling.
Support
Furukawa Electric Customer Support Center handles maintenance to ensure the safe and secure use of lasers. It also offers a variety of customer training programs, which include explanations on product handling instructions, troubleshooting, and practical training for service part replacement and repair methods.
Related news releases
Furukawa Electric and Furukawa Develop World-leading Laser Welding Technology for Pure Copper
Realizing Higher Quality Welding in Aluminum Materials Used for Automobiles
Furukawa Electric Group’s efforts towards the SDGs
Based on the corporate philosophy of “Drawing on more than a century of expertise in the development and fabrication of advanced materials to contribute to the realization of a sustainable society through continuous technological innovation,” the Furukawa Electric Group is conducting business activities centered on four core technological capabilities (metals, polymers, photonics and high frequency). Moreover, keeping in mind the “Sustainable Development Goals (SDGs)” adopted by the UN, we formulated the “Furukawa Electric Group Vision 2030,” which clarified the business areas of the Furukawa Electric Group, and are advancing efforts aimed at “creating solutions for the new generation of global infrastructure combining information, energy, and mobility to build a sustainable world and make people’s life safe, peaceful, and rewarding.
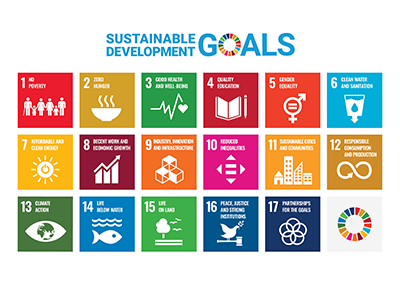