CHALLENGE
EPISODE
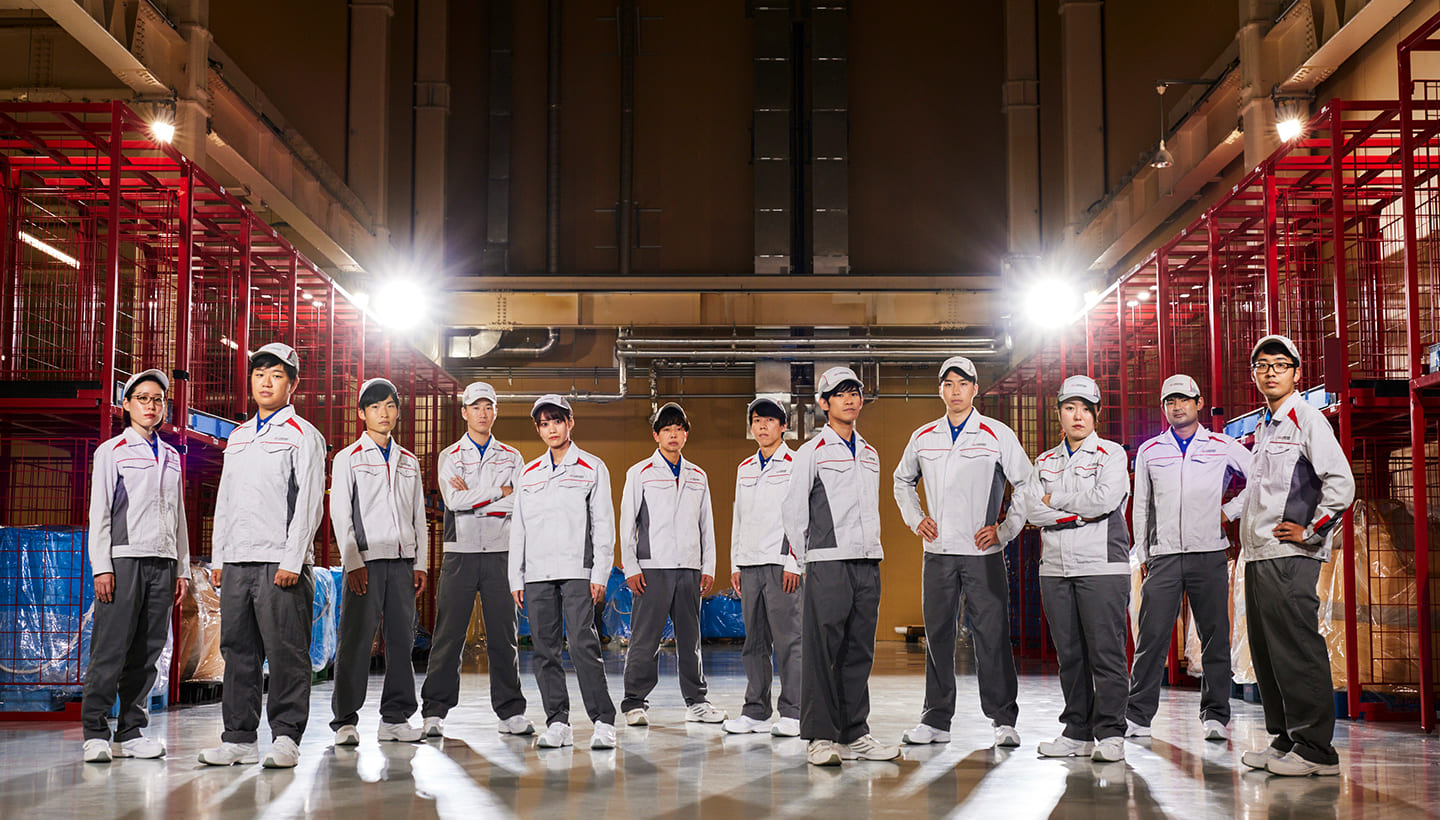

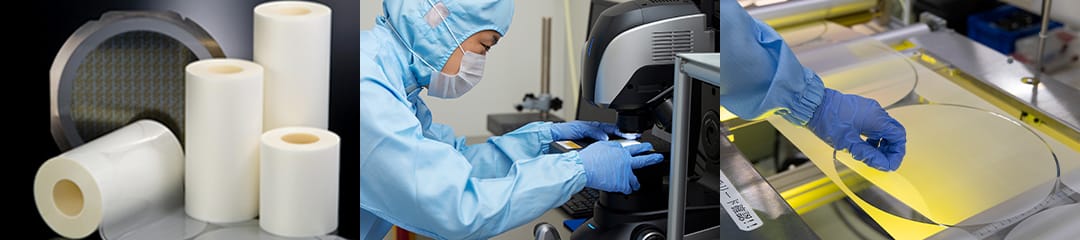
-
AT製造部 平塚生産技術課/2020年入社
テープ製造において重要な厚み精度に大きく影響する塗工工程を担当。[写真左]
-
AT開発部 技術課/2017年入社
先端加工プロセス向けのBGテープの開発を担当。[写真中央]
-
AT品質保証部 平塚品質保証課/2019年入社
お客様の期待する品質を保証するための検査技術の確立を担当。現在は開発部に所属。[写真右]
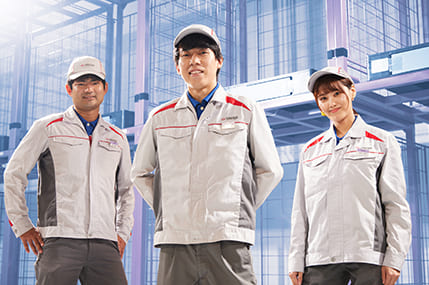
-
AT製造部 生産技術課/2020年入社
外部の協力会社と連携し薄膜技術の確立を担当。[写真左]
-
AT品質保証部 三重品質保証課/2021年入社
直材と放熱特性を保証する新しい検査技術の確立を担当。[写真中央]
-
AT製造部 三重生産技術課/2018年入社
外部の協力会社と連携し薄膜技術の確立を担当している。現在は技術営業部に所属。[写真右]
-
AT開発部 AT開発課/2017年入社
先端半導体ニーズに対応した高機能製品を付加した自社DAFの開発を担当。
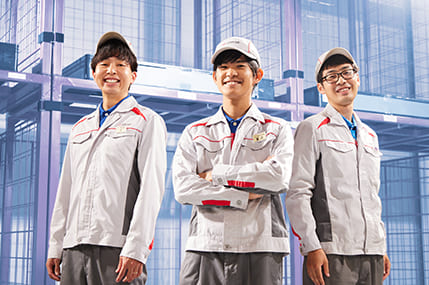
-
AT開発部 開発課/2018年入社
高機能接着フィルムの半導体製造以外への展開を担当。[写真左]
-
AT技術営業部 粘着テープ営業課/2022年入社
BG/DCテープの半導体製造以外への展開を担当。[写真中央]
-
AT開発部 技術課/2019年入社
半導体製造以外に適用されるDCテープの開発を担当。[写真右]
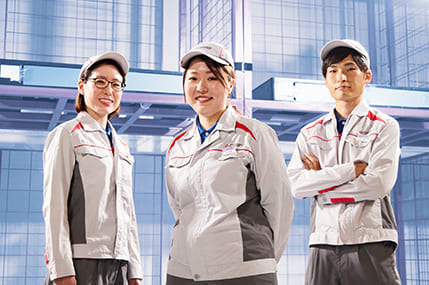
-
AT製造部 設備技術課/2020年入社
製品を安定製造するための設備保全、改造を担当。[写真左]
-
AT製造部 三重生産技術課/2019年入社
製品化に向けて安定した量産ができる仕組みづくりを担当。[写真中央]
-
AT製造部 平塚生産技術課/2021年入社
製品化に向けて安定した量産ができる仕組みづくりを担当。[写真右]
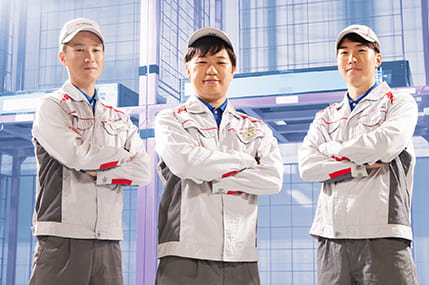
※所属は2023年10月現在
-
先端加工プロセスチーム
「チーム一丸となって
先端分野でのスペックインを実現」
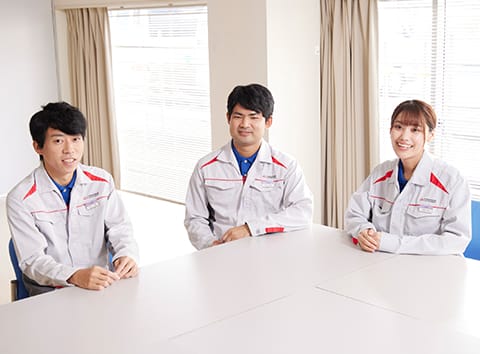
-
高機能接着フィルムチーム
「新技術を積極的に取り込み、
最先端の製品開発へ」
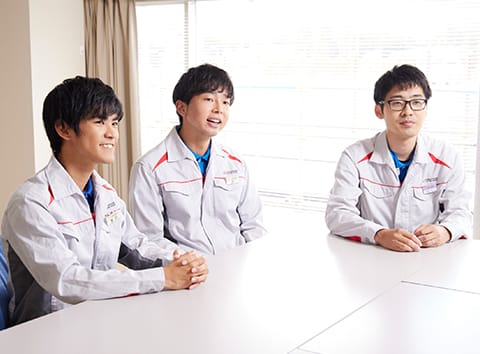
-
技術応用チーム
「半導体分野以外での挑戦。
それは持続可能な社会の実現にも
つながっている」
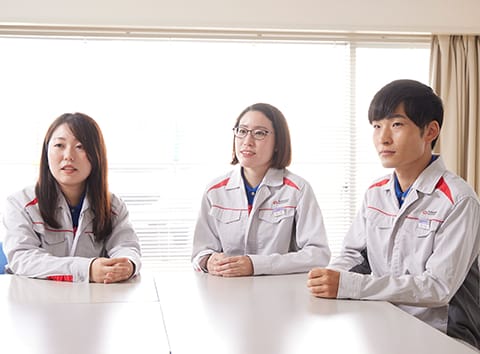
-
ものづくり変革チーム
「チームで取り組む“ものづくり力”
向上が
未来を支える」
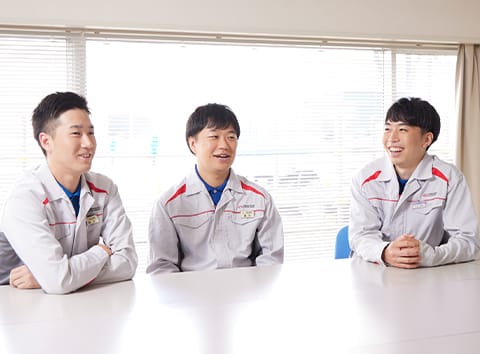

社会の発展に不可欠な基盤の
躍進を支え、
つながる未来をつくっていく。
他のエピソードはこちら